Preparation method of polyamide composite material applied to oil pipeline
A composite material and oil pipeline technology, applied in the field of composite materials, can solve the problems of low impact strength at low temperature, affect the electrical properties of materials, large water absorption, etc., achieve high temperature resistance and mechanical properties, improve anti-corrosion properties, and increase the interlayer. effect of spacing
- Summary
- Abstract
- Description
- Claims
- Application Information
AI Technical Summary
Problems solved by technology
Method used
Image
Examples
Example Embodiment
[0026] Example 1
[0027] A preparation method of polyamide composite material for oil pipeline, including the following steps:
[0028] (1) Sun-dried and crushed the earthen wattle bark, and sieved through a 200-300 mesh sieve to obtain the earthen wattle bark powder;
[0029] (2) Soak the wattle bark powder prepared above in a mixed aqueous solution of sodium citrate and hydrogen peroxide for 30 minutes, then sonicate for 30 minutes at a power of 500W, and finally undergo plasma treatment in the cavity of the oxygen plasma device to obtain Pre-treated soil wattle bark powder;
[0030] Among them, the mass concentration of sodium citrate in the mixed aqueous solution is 30%, and the mass concentration of hydrogen peroxide is 45%; the dosage ratio of the mixed aqueous solution of wattle bark powder and sodium citrate and hydrogen peroxide is 1g:70mL;
[0031] (3) Disperse the pretreated earthen bark powder prepared above in an organic solvent, add hexafluorobutyl methacrylate after heatin
Example Embodiment
[0037] Example 2
[0038] A preparation method of polyamide composite material for oil pipeline, including the following steps:
[0039] (1) Sun-dried and crushed the earthen wattle bark, and sieved through a 200-300 mesh sieve to obtain the earthen wattle bark powder;
[0040] (2) Soak the wattle bark powder prepared above in a mixed aqueous solution of sodium citrate and hydrogen peroxide for 30 minutes, then sonicate for 30 minutes at a power of 500W, and finally undergo plasma treatment in the cavity of the oxygen plasma device to obtain Pre-treated soil wattle bark powder;
[0041] Among them, the mass concentration of sodium citrate in the mixed aqueous solution is 30%, and the mass concentration of hydrogen peroxide is 45%; the dosage ratio of the mixed aqueous solution of wattle bark powder and sodium citrate and hydrogen peroxide is 1g:100mL;
[0042] (3) Disperse the pretreated earthen bark powder prepared above in an organic solvent, add hexafluorobutyl methacrylate after heati
Example Embodiment
[0048] Example 3
[0049] A preparation method of polyamide composite material for oil pipeline, including the following steps:
[0050] (1) Sun-dried and pulverized soil wattle bark, and passed through a 200-300 mesh sieve to obtain soil wattle bark powder;
[0051] (2) Soak the wattle bark powder obtained above in a mixed aqueous solution of sodium citrate and hydrogen peroxide for 30 minutes, then ultrasonicate for 30 minutes at a power of 500W, and finally plasma treatment in the cavity of the oxygen plasma device to obtain Pre-treated soil wattle bark powder;
[0052] Among them, the mass concentration of sodium citrate in the mixed aqueous solution is 30%, and the mass concentration of hydrogen peroxide is 45%; the dosage ratio of the mixed aqueous solution of wattle bark powder and sodium citrate and hydrogen peroxide is 1g:80mL;
[0053] (3) Disperse the pretreated earthen bark powder prepared above in an organic solvent, add hexafluorobutyl methacrylate after the temperature is r
PUM
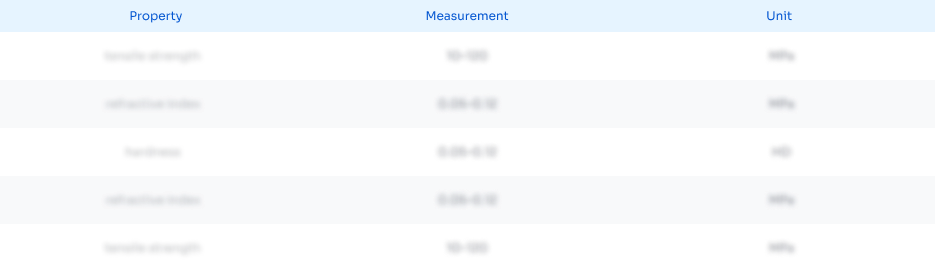
Abstract
Description
Claims
Application Information
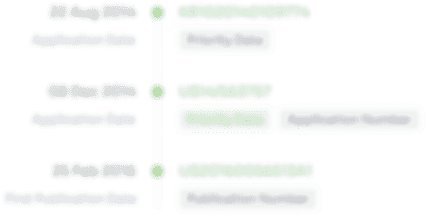
- R&D Engineer
- R&D Manager
- IP Professional
- Industry Leading Data Capabilities
- Powerful AI technology
- Patent DNA Extraction
Browse by: Latest US Patents, China's latest patents, Technical Efficacy Thesaurus, Application Domain, Technology Topic.
© 2024 PatSnap. All rights reserved.Legal|Privacy policy|Modern Slavery Act Transparency Statement|Sitemap