Marine environment resistant metamaterial substrate and preparation method thereof
A marine environment and metamaterial technology, applied in the field of materials, can solve problems such as poor performance, high cost, and low efficiency
- Summary
- Abstract
- Description
- Claims
- Application Information
AI Technical Summary
Problems solved by technology
Method used
Image
Examples
preparation example Construction
[0029] The method for preparing a marine environment-resistant metamaterial base material provided by the present invention is to prepare a metamaterial base material by mixing ceramic powder and additives in a raw rubber matrix, specifically comprising the following steps: mixing raw rubber, ceramic powder, and vulcanizing agent Blending with additives in proportion; followed by banbury blending and thermocompression molding to prepare the marine environment-resistant metamaterial base material.
[0030] figure 1 It is a process flow diagram of a method for preparing a metamaterial base material resistant to a marine environment according to a preferred embodiment of the present invention. Such as figure 1 As shown, the elastomer powder, ceramic powder, and silane coupling agent are first blended in proportion, and the contents of each component are: 100 parts of raw rubber, 40-330 parts of ceramic powder, 0.7-6 parts of vulcanizing agent and 0.4-15 parts of additives, optiona
Embodiment 1
[0033] After blending 100 parts of EPDM rubber, 40 parts of SiC ceramic powder, 1 part of dicumyl peroxide, 0.5 part of stearic acid, 0.5 part of anti-aging agent and 0.5 part of silane coupling agent, put it into the mixer In the machine, banbury blending is carried out at a temperature of 70°C to make the components evenly mixed; the mixture obtained after banbury mixing and blending is put into a flat-plate hot press machine for hot press molding, wherein the pressure of hot press molding 25MPa, hot-pressed at 170°C for 10 minutes, and dried to obtain a marine environment-resistant metamaterial substrate. The prepared marine environment-resistant metamaterial substrate can have different thicknesses and can be attached.
Embodiment 2
[0035] 100 parts of nitrile rubber, 150 parts of BaTiO 3Ceramic powder and 2 parts of dicumyl peroxide, 1 part of stearic acid, 1 part of anti-aging agent, and 1 part of silane coupling agent are ball-milled and blended in a full-range planetary ball mill. After blending, the mixture is put into a compact In the mixer, banbury blending is carried out at a temperature of 60°C, so that the components are mixed uniformly; the mixture obtained after banbury blending is put into a hot press machine, and hot press molding, wherein, the pressure of hot press molding 20MPa, hot-pressed at 150°C for 30 minutes, and dried to obtain a marine environment-resistant metamaterial substrate. The prepared marine environment-resistant metamaterial substrate can have different thicknesses and can be attached.
PUM
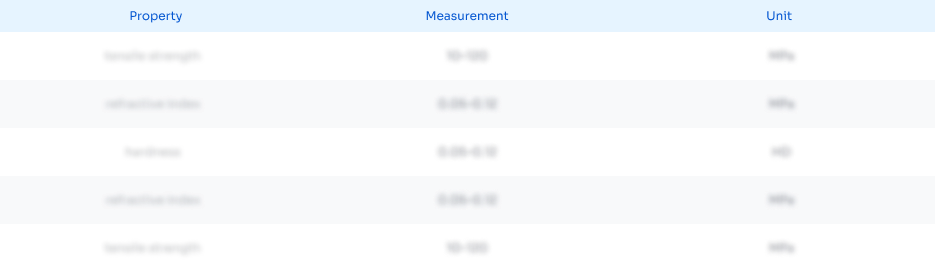
Abstract
Description
Claims
Application Information
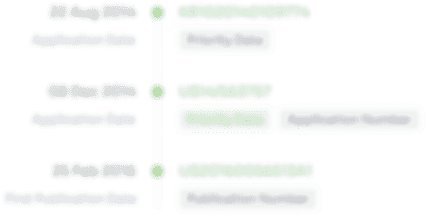
- R&D Engineer
- R&D Manager
- IP Professional
- Industry Leading Data Capabilities
- Powerful AI technology
- Patent DNA Extraction
Browse by: Latest US Patents, China's latest patents, Technical Efficacy Thesaurus, Application Domain, Technology Topic.
© 2024 PatSnap. All rights reserved.Legal|Privacy policy|Modern Slavery Act Transparency Statement|Sitemap