Aluminum alloy casting moulding sand and preparing method thereof
A technology of casting molds and aluminum alloys, which is applied in casting molding equipment, casting molds, metal processing equipment, etc., can solve the problems of casting quality decline and poor performance, so as to improve the yield of castings, reduce the cost of castings, and improve the pressure resistance. Effect
- Summary
- Abstract
- Description
- Claims
- Application Information
AI Technical Summary
Problems solved by technology
Method used
Examples
Example Embodiment
[0014] Example one:
[0015] The casting sand components include 20 parts by weight of quartz sand, 10 parts of Hao sand, 10 parts of corundum sand, 5 parts of graphite powder, 5 parts of bentonite, 5 parts of diatomaceous earth, 2 parts of hollow microbeads, 3 parts of glass fiber, 4 parts of clay, 2 parts of light calcined powder, 10 parts of furan resin, 2 parts of polypropylene fiber.
[0016] The preparation method of this embodiment includes the following steps:
[0017] A. Mix the quartz sand, Hao sand, corundum sand, and graphite powder and add them to the sand mixer to obtain a mixture A;
[0018] B. Preheat the mixture A, the preheating temperature is 50℃, the preheating time is 20min, then add bentonite, diatomaceous earth, clay, lightly burned powder, furan resin, mix and stir at high speed at 4000 rpm / Min, stirring time is 25min, to obtain mixture B;
[0019] C. Add hollow microbeads, glass fibers, and polypropylene fibers to the mixture B, fully stir and mix for 5 hours,
Example Embodiment
[0020] Embodiment two:
[0021] The casting sand components include 40 parts by weight of quartz sand, 20 parts of Hao sand, 30 parts of corundum sand, 10 parts of graphite powder, 15 parts of bentonite, 18 parts of diatomaceous earth, 6 parts of hollow microbeads, 6 parts of glass fiber, 12 parts of clay, 8 parts of light burnt powder, 18 parts of furan resin, 4 parts of polypropylene fiber.
[0022] The preparation method of this embodiment includes the following steps:
[0023] A. Mix the quartz sand, Hao sand, corundum sand, and graphite powder and add them to the sand mixer to obtain a mixture A;
[0024] B. Preheat the mixture A, the preheating temperature is 50℃, the preheating time is 20min, then add bentonite, diatomaceous earth, clay, lightly burned powder, furan resin, mix and stir at high speed at 4000 rpm / Min, stirring time is 25min, to obtain mixture B;
[0025] C. Add hollow microbeads, glass fibers, and polypropylene fibers to the mixture B, fully stir and mix for 5 ho
Example Embodiment
[0026] Embodiment three:
[0027] The casting sand components include 25 parts by weight of quartz sand, 12 parts of Hao sand, 15 parts of corundum sand, 6 parts of graphite powder, 6 parts of bentonite, 8 parts of diatomaceous earth, 3 parts of hollow microbeads, 4 parts of glass fiber, 6 parts of clay, 3 parts of light burnt powder, 12 parts of furan resin, 3 parts of polypropylene fiber.
[0028] The preparation method of this embodiment includes the following steps:
[0029] A. Mix the quartz sand, Hao sand, corundum sand, and graphite powder and add them to the sand mixer to obtain a mixture A;
[0030] B. Preheat the mixture A, the preheating temperature is 50℃, the preheating time is 20min, then add bentonite, diatomaceous earth, clay, lightly burned powder, furan resin, mix and stir at high speed at 4000 rpm / Min, stirring time is 25min, to obtain mixture B;
[0031] C. Add hollow microbeads, glass fibers, and polypropylene fibers to the mixture B, fully stir and mix for 5 hour
PUM
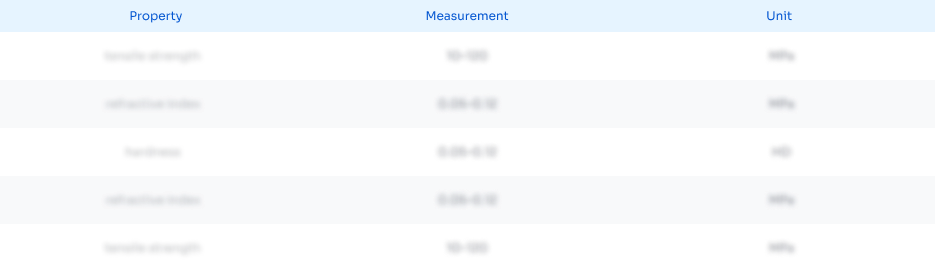
Abstract
Description
Claims
Application Information
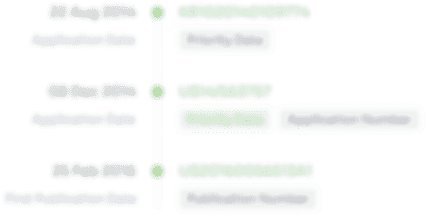
- R&D Engineer
- R&D Manager
- IP Professional
- Industry Leading Data Capabilities
- Powerful AI technology
- Patent DNA Extraction
Browse by: Latest US Patents, China's latest patents, Technical Efficacy Thesaurus, Application Domain, Technology Topic.
© 2024 PatSnap. All rights reserved.Legal|Privacy policy|Modern Slavery Act Transparency Statement|Sitemap