Continuous production equipment of copolymerized flame retardant monomer and production method thereof
A technology of flame retardant monomer and production method, applied in the field of production equipment of flame retardant monomer, can solve problems such as low device efficiency and product batch quality difference, and achieve high reaction efficiency and production efficiency, stable product quality, manual labor Action-less effect
- Summary
- Abstract
- Description
- Claims
- Application Information
AI Technical Summary
Benefits of technology
Problems solved by technology
Method used
Image
Examples
Embodiment 1
[0020] Example 1: A continuous production equipment for a copolymerized flame retardant monomer, including a solid flame retardant silo, a weight loss scale, a screw feeder, an ethylene glycol flow meter, an additive preparation tank, a filter screen, and an additive storage Tanks, metering pumps, beating kettles, atmospheric pressure esterification kettles, negative pressure esterification kettles and rectification towers, the solid flame retardant silo is connected to a weight loss scale as a solid continuous metering device, and then connected to a screw feeder to provide Continuous flame retardant powder, at the same time, the auxiliary agent preparation tank is connected to the auxiliary agent storage tank through the filter screen, and then provides continuous ethylene glycol solution for the beating kettle through the metering pump, and the beating kettle is connected to the normal pressure esterification kettle and the negative pressure The esterification kettle uses the p
Embodiment 2
[0026] Embodiment 2: The continuous production equipment of the copolymerized flame retardant monomer is the same as that of Embodiment 1, and the different continuous production processes are:
[0027] Batching stage: The flow rate is set according to the molar ratio of flame retardant to EG of 1:3, and the flame retardant is HMPPA; the input amount of ether inhibitor and stabilizer is 5ppm and 800ppm of the mass content of the final product respectively.
[0028] Reaction stage: The esterification reaction temperature of the atmospheric pressure esterification tank is 170°C, and the residence time is 1.5h. The pressure of the negative pressure esterification tank is 60kPa, the reaction temperature is 190°C, and the residence time is 0.5h.
[0029] Finished product cooling stage: the flame retardant monomer is continuously extracted from the negative pressure reactor with a transfer pump, and is cooled and transported to the finished product tank with a heat exchanger in the mid
Embodiment 3
[0031] Embodiment 3: The continuous production equipment of the copolymerized flame retardant monomer is the same as that of Embodiment 1, and the different continuous production processes are:
[0032] Batching stage: The flow rate is set according to the molar ratio of flame retardant to EG of 1:5, and the flame retardants are CEPPA and BCPPO; the input amount of ether inhibitor and stabilizer is 5ppm and 400ppm of the final product mass content respectively
[0033] Esterification stage: the esterification reaction temperature of the normal pressure reactor is 150°C, and the residence time is 3h. The pressure of the negative pressure esterification tank is 30kPa, the reaction temperature is 150°C, and the residence time is 2h.
[0034] Finished product cooling stage: the flame retardant monomer is continuously extracted from the negative pressure reactor with a transfer pump, and is cooled and transported to the finished product tank with a heat exchanger in the middle.
[00
PUM
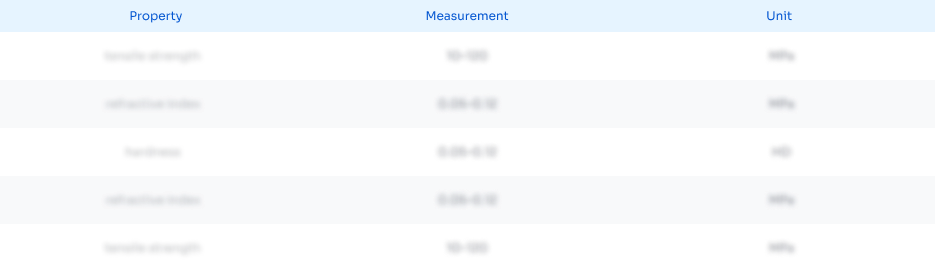
Abstract
Description
Claims
Application Information
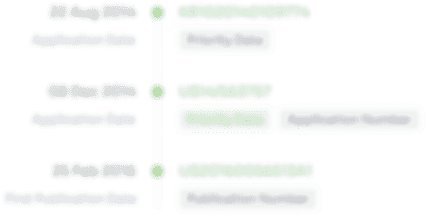
- R&D Engineer
- R&D Manager
- IP Professional
- Industry Leading Data Capabilities
- Powerful AI technology
- Patent DNA Extraction
Browse by: Latest US Patents, China's latest patents, Technical Efficacy Thesaurus, Application Domain, Technology Topic.
© 2024 PatSnap. All rights reserved.Legal|Privacy policy|Modern Slavery Act Transparency Statement|Sitemap