Preparation method of magnetic carbon material
A magnetic carbon, mass ratio technology, applied in chemical instruments and methods, alkali metal oxides/hydroxides, inorganic chemistry, etc., can solve the problems of waste water preparation process, expensive and complicated equipment, and achieve simple process route and environmental protection. The effect of low pollution and excellent lithium storage performance
- Summary
- Abstract
- Description
- Claims
- Application Information
AI Technical Summary
Benefits of technology
Problems solved by technology
Method used
Image
Examples
Embodiment 1
[0018] Ferrocene and red phosphorus are used as raw materials, and the two are uniformly mixed according to the mass ratio of 1.5:1, and then placed in a closed reactor with an oxygen content of 21% for heat treatment. The heating mechanism is as follows: firstly, the temperature is raised to 450°C at a rate of 3°C / min, and then the temperature is kept at a constant temperature for 4 hours, and then naturally cooled to room temperature. Open the kettle to take out the reaction product, heat it at a temperature of 50°C to initiate combustion, and the collected black fluffy combustion product is a magnetic carbon material. The material is used as the negative electrode material of the lithium ion battery, and the reversible capacity of 554 mAh / g can be maintained after 500 charge-discharge cycles at a current density of 100 mA / g.
Embodiment 2
[0020] Ferrocene and red phosphorus are used as raw materials, and the two are uniformly mixed according to the mass ratio of 0.5:1, and then placed in a closed reactor with an oxygen content of 5% for heat treatment. The heating mechanism is as follows: first, the temperature was raised to 400°C at a rate of 5°C / min, and then the temperature was kept at a constant temperature for 1 hour, and then naturally cooled to room temperature. Open the kettle to take out the reaction product, heat it at 40°C to initiate combustion, and the collected black fluffy combustion product is a magnetic carbon material. The material is used as the negative electrode material of the lithium ion battery, and the reversible capacity of 502 mAh / g can be maintained after 500 charge-discharge cycles at a current density of 100 mA / g.
Embodiment 3
[0022] Ferrocene and red phosphorus are used as raw materials, and the two are uniformly mixed according to the mass ratio of 2:1, and then placed in a closed reaction kettle with an oxygen content of 15% for heat treatment. The heating mechanism is as follows: first, the temperature is raised to 500°C at a rate of 2°C / min, and then the temperature is kept at a constant temperature for 4 hours, and then naturally cooled to room temperature. Open the kettle to take out the reaction product, heat it at 80°C to initiate combustion, and the collected black fluffy combustion product is a magnetic carbon material. The material is used as the negative electrode material of the lithium ion battery, and the reversible capacity of 529 mAh / g can be maintained after 500 charge-discharge cycles at a current density of 100 mA / g.
PUM
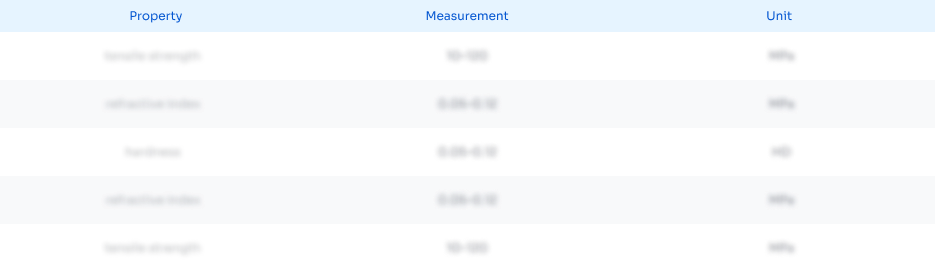
Abstract
Description
Claims
Application Information
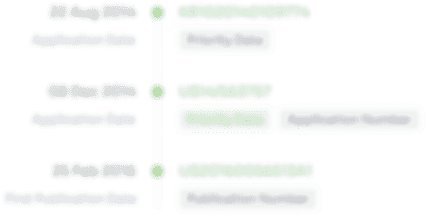
- R&D Engineer
- R&D Manager
- IP Professional
- Industry Leading Data Capabilities
- Powerful AI technology
- Patent DNA Extraction
Browse by: Latest US Patents, China's latest patents, Technical Efficacy Thesaurus, Application Domain, Technology Topic.
© 2024 PatSnap. All rights reserved.Legal|Privacy policy|Modern Slavery Act Transparency Statement|Sitemap