Waterproof and heat-preservation lunch bag processing material
A technology of processing materials and waterproof fabrics, which is applied to the types of packaging items, applications, special packaging items, etc., can solve the problems of shortening the service life of lunch bags, limited insulation effect of lunch bags, and affecting insulation effects, etc., to achieve excellent waterproof effect and heat preservation Good effect and long service life
- Summary
- Abstract
- Description
- Claims
- Application Information
AI Technical Summary
Problems solved by technology
Method used
Image
Examples
Embodiment 1
[0026] Preparation of lunch bag processing materials: It consists of a waterproof inner layer, an insulating middle layer and a decorative outer layer. The waterproof inner layer is made of PVC film, and the decorative outer layer is made of PTFE film and Oxford cloth.
[0027] Processing of insulation middle layer:
[0028] (1) 30g of asbestos wool and 10g of sepiolite fiber powder are mixed and then placed in an oven at 110-120°C and dried to constant weight to obtain material I;
[0029] (2) Heat 5g of microcrystalline wax to a molten state and keep stirring, add 5g of magnesium aluminum silicate and 1g of polytetrafluoroethylene superfine powder, and stir evenly to obtain material II;
[0030] (3) Heat 20g of gelling agent to 120-130°C and keep stirring, then add material II and 1g cationic polyacrylamide, stir evenly, then add material I, stir evenly again, and cool down at a rate of 5-10°C / min Speed cooling to 0-10 ℃ and heat preservation for more than 30 minutes to ob
Embodiment 2
[0033] Preparation of lunch bag processing materials: It consists of a waterproof inner layer, an insulating middle layer and a decorative outer layer. The waterproof inner layer is made of PVC film, and the decorative outer layer is made of PTFE film and Oxford cloth.
[0034] Processing of insulation middle layer:
[0035] (1) After mixing 40g of asbestos wool and 15g of sepiolite fiber powder, place it in an oven at 110-120°C and dry to constant weight to obtain material I;
[0036] (2) Heat 5g of microcrystalline wax to a molten state and keep stirring, add 5g of magnesium aluminum silicate and 2g of polytetrafluoroethylene superfine powder, and stir evenly to obtain material II;
[0037] (3) Heat 20g of gelling agent to 120-130°C and keep stirring, then add material II and 2g of cationic polyacrylamide, stir evenly, then add material I, stir evenly again, and cool down at a rate of 5-10°C / min Speed cooling to 0-10 ℃ and heat preservation for more than 30 minutes to obta
Embodiment 3
[0040] Preparation of lunch bag processing materials: It consists of a waterproof inner layer, an insulating middle layer and a decorative outer layer. The waterproof inner layer is made of PVC film, and the decorative outer layer is made of PTFE film and Oxford cloth.
[0041] Processing of insulation middle layer:
[0042] (1) After mixing 40g of asbestos wool and 15g of sepiolite fiber powder, place it in an oven at 110-120°C and dry to constant weight to obtain material I;
[0043] (2) Heat 5g of microcrystalline wax to a molten state and keep stirring, add 5g of magnesium aluminum silicate and 2g of polytetrafluoroethylene superfine powder, and stir evenly to obtain material II;
[0044] (3) Heat 20g of gelling agent to 120-130°C and keep stirring, then add material II and 2g of cationic polyacrylamide, stir evenly, then add material I, stir evenly again, and cool down at a rate of 5-10°C / min Speed cooling to 0-10 ℃ and heat preservation for more than 30 minutes to obta
PUM
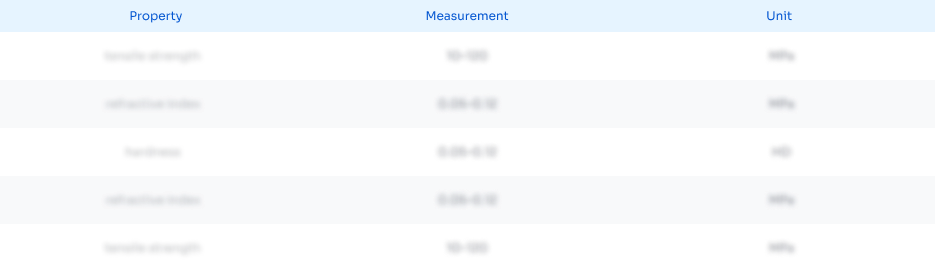
Abstract
Description
Claims
Application Information
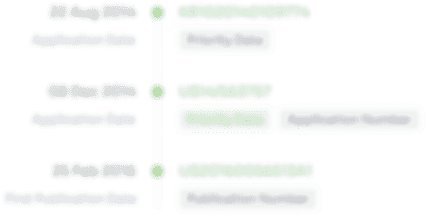
- R&D Engineer
- R&D Manager
- IP Professional
- Industry Leading Data Capabilities
- Powerful AI technology
- Patent DNA Extraction
Browse by: Latest US Patents, China's latest patents, Technical Efficacy Thesaurus, Application Domain, Technology Topic.
© 2024 PatSnap. All rights reserved.Legal|Privacy policy|Modern Slavery Act Transparency Statement|Sitemap