Cleaning and prefilming agent and preparation method and application thereof
A technology of pre-filming agent and inorganic film, which is applied in the field of water treatment agent, preparation of cleaning pre-filming agent, and cleaning pre-filming agent, can solve the problems of environmental eutrophication pollution, complicated pre-filming treatment process, etc. The effect of strong anti-fouling effect and strong corrosion resistance
- Summary
- Abstract
- Description
- Claims
- Application Information
AI Technical Summary
Problems solved by technology
Method used
Image
Examples
Embodiment 1
[0024] This embodiment provides a cleaning pre-film agent for circulating cooling water system, the mass percentage of each component is as follows:
[0025] Salicylic acid: 20%;
[0026] Sodium gluconate: 15%;
[0027] Polyepoxysuccinic acid: 10%;
[0028] Zinc sulfate monohydrate: 4%;
[0029] Disodium EDTA: 3%;
[0030] Potassium hydroxide: 25%;
[0031] Deionized water: 23%.
[0032] The preparation method of cleaning pre-film agent described in this embodiment:
[0033] First add 4kg of zinc sulfate monohydrate, 15kg of sodium gluconate, 3kg of disodium ethylenediaminetetraacetic acid and 23kg of deionized water into the stirring reactor, start stirring, and then add 20kg of salicylic acid, 10kg of poly Stir the epoxysuccinic acid evenly, and finally add 25kg of potassium hydroxide to adjust the pH to neutral, and stir for 20-30min to obtain the cleaning and pre-filming agent.
Embodiment 2
[0035] This embodiment provides a cleaning pre-film agent for circulating cooling water system, the mass percentage of each component is as follows:
[0036] Tartaric acid: 18%;
[0037] Sodium gluconate: 10%;
[0038] Polyepoxysuccinic acid: 8%;
[0039] Zinc chloride: 5%;
[0040] Sodium iminodisuccinate: 2%;
[0041] Sodium hydroxide: 23%;
[0042] Deionized water: 34%.
[0043] The preparation method of cleaning pre-film agent described in this embodiment:
[0044]First add 5kg of zinc chloride, 10kg of sodium gluconate, 2kg of sodium iminodisuccinate and 34kg of deionized water into the stirring reactor, start stirring, and after all are dissolved, then add 18kg of tartaric acid and 8kg of polyepoxysuccinic acid in sequence Stir evenly, and finally add 23 kg of potassium hydroxide to adjust the pH to neutral, and stir for 20-30 minutes to obtain the cleaning and pre-filming agent.
Embodiment 3
[0046] This embodiment provides a cleaning pre-film agent for circulating cooling water system, the mass percentage of each component is as follows:
[0047] Citric acid: 15%;
[0048] Sodium gluconate: 20%;
[0049] Polyaspartic acid: 10%;
[0050] Zinc sulfate monohydrate: 8%;
[0051] Sodium aminotriacetate: 4%;
[0052] Sodium hydroxide: 18%;
[0053] Deionized water: 25%.
[0054] The preparation method of cleaning pre-film agent described in this embodiment:
[0055] First add 8kg of zinc sulfate monohydrate, 20kg of sodium gluconate, 4kg of sodium aminotriacetate and 25kg of deionized water into the stirring reactor, start stirring, and after all are dissolved, then add 15kg of citric acid and 10kg of polyaspartic acid in sequence Stir evenly, and finally add 18kg of sodium hydroxide to adjust the pH to neutral, and stir for 20-30 minutes to obtain the cleaning and pre-filming agent.
PUM
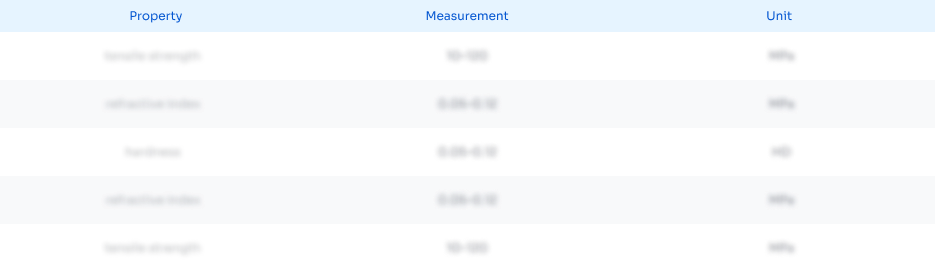
Abstract
Description
Claims
Application Information
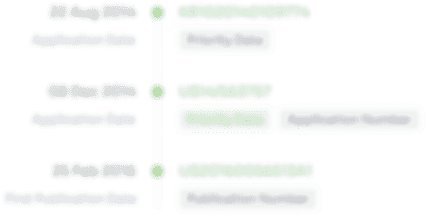
- R&D Engineer
- R&D Manager
- IP Professional
- Industry Leading Data Capabilities
- Powerful AI technology
- Patent DNA Extraction
Browse by: Latest US Patents, China's latest patents, Technical Efficacy Thesaurus, Application Domain, Technology Topic.
© 2024 PatSnap. All rights reserved.Legal|Privacy policy|Modern Slavery Act Transparency Statement|Sitemap