Matrix self-cleaning method in CVD diamond deposition process
A deposition process, diamond technology, applied in metal material coating process, gaseous chemical plating, coating, etc., can solve the problems that the substrate cannot be 100% clean, low nucleation density, poor film quality, etc., to improve Nucleation rate, no surface defects, full grain effect
- Summary
- Abstract
- Description
- Claims
- Application Information
AI Technical Summary
Benefits of technology
Problems solved by technology
Method used
Image
Examples
Embodiment 1
[0025] The present embodiment provides the substrate self-cleaning method in the CVD diamond deposition process of the present invention, specifically:
[0026] Step 1. Arrange the substrate and hot wire in the CVD vacuum deposition furnace, pump to the ultimate vacuum, and keep it for 5 minutes;
[0027] Step 2. Feed methane and hydrogen into the CVD vacuum deposition furnace; the flow of methane is 50 sccm, the flow of hydrogen is 2000 sccm, and the pressure of the reaction chamber in the CVD vacuum deposition furnace can be adjusted to 3KPa through a regulating valve.
[0028] Step 3. Light up the heating wire, and after the voltage of the heating wire is increased to 40V, observe the color change of the heating wire and the substrate color; about 5 minutes after the voltage is increased to the set value, the surface of the substrate produces color patterns, indicating that The graphite has been attached to the surface of the substrate, and crystal nuclei have begun to form;
Embodiment 2
[0032] The present embodiment provides the substrate self-cleaning method in the CVD diamond deposition process of the present invention, specifically:
[0033] Step 1. Arrange the substrate and hot wire in the CVD vacuum deposition furnace, pump to the ultimate vacuum, and keep it for 3 minutes;
[0034] Step 2. Feed methane and hydrogen into the CVD vacuum deposition furnace; the flow of methane is 80 sccm, the flow of hydrogen is 3000 sccm, and the pressure of the reaction chamber in the CVD vacuum deposition furnace can be adjusted to 2KPa through a regulating valve.
[0035] Step 3. Light up the heating wire, and after the voltage of the heating wire is increased to 30V, observe the color change of the heating wire and the substrate color; about 5 minutes after the voltage is raised to the set value, the surface of the substrate produces color patterns, indicating that The graphite has been attached to the surface of the substrate, and crystal nuclei have begun to form;
[
Embodiment 3
[0039] The present embodiment provides the substrate self-cleaning method in the CVD diamond deposition process of the present invention, specifically:
[0040] Step 1. Arrange the substrate and hot wire in the CVD vacuum deposition furnace, pump to the ultimate vacuum, and keep it for 8 minutes;
[0041] Step 2. Feed methane and hydrogen into the CVD vacuum deposition furnace; the flow of methane is 30 sccm, the flow of hydrogen is 1500 sccm, and the pressure of the reaction chamber in the CVD vacuum deposition furnace can be adjusted to 4KPa through a regulating valve.
[0042] Step 3. Light up the heating wire, and after the voltage of the heating wire is increased to 50V, observe the color change of the heating wire and the substrate color; about 5 minutes after the voltage is raised to the set value, the surface of the substrate produces color lines, indicating that The graphite has been attached to the surface of the substrate, and crystal nuclei have begun to form;
[004
PUM
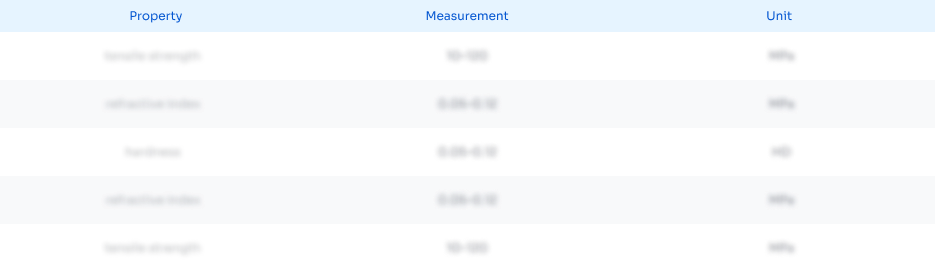
Abstract
Description
Claims
Application Information
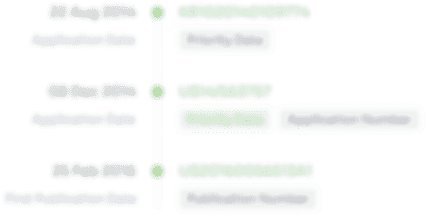
- R&D Engineer
- R&D Manager
- IP Professional
- Industry Leading Data Capabilities
- Powerful AI technology
- Patent DNA Extraction
Browse by: Latest US Patents, China's latest patents, Technical Efficacy Thesaurus, Application Domain, Technology Topic.
© 2024 PatSnap. All rights reserved.Legal|Privacy policy|Modern Slavery Act Transparency Statement|Sitemap