Stainless steel separation piece and preparation method thereof
A technology of stainless steel and spacers, which is applied in the direction of gaseous chemical plating, metal material coating process, coating, etc., can solve the problems affecting the quality of diamond saw blades, the life of stainless steel spacers, the appearance of diamond saw blades, and troublesome operation. Achieve long service life, short time required and good molding quality
- Summary
- Abstract
- Description
- Claims
- Application Information
AI Technical Summary
Benefits of technology
Problems solved by technology
Method used
Examples
preparation example Construction
[0028] A preparation method of a stainless steel spacer, comprising the following specific steps:
[0029] a. Wash and dry both sides of the stainless steel plate with acetone;
[0030] b. Prepare a mixed ethanol solution containing at least one of nickel nitrate, copper nitrate, cobalt nitrate, molybdenum nitrate, tantalum nitrate, niobium nitrate and transition metal nitrates of iron nitrate and chromium nitrate;
[0031] C, the mixed ethanol solution of multiple nitrates is sprayed equably on the stainless steel plate surface that step a handles, dries, sprays again, dries again, reaches set value until reaching stainless steel plate surface nitrate loading capacity;
[0032] d. Place the stainless steel plate with nitrate coating on the surface in a CVD reaction furnace isolated from oxygen, preheat it to 700-800°C with nitrogen gas, and feed gaseous hydrocarbons, and at the same time, hydrogen sulfide / hydrogen (use necessary Component hydrogen dilutes hydrogen sulfide), o
Embodiment 1
[0036] Preparation of ethanol solution of nitrate: (weight ratio, iron nitrate: chromium nitrate: nickel nitrate=1:0.5:3; ethanol solution concentration 10wt%). Spraying ethanol solution of nitrate: spraying amount 1.7mg / cm 2 .
[0037] Hang the cleaned and dried stainless steel 321 plate as a CVD substrate (size: 105 mm in diameter) horizontally in an oxygen-isolated reaction furnace, preheat to 750°C with 3.8 sccm per square centimeter of substrate, and start to use hydrogen (flow rate: Substrate 3.4sccm per square centimeter) and hydrogen sulfide (flow rate: 0.003sccm per square centimeter substrate) are introduced into the reaction furnace to reduce the nitrate in the hydrogen sulfide-hydrogen atmosphere for 5 minutes, and maintain the gas flow rate; then apply 5V, 100mA, 200Hz AC The current is on the stainless steel plate, and at the same time, acetylene is passed through at a flow rate of 1.5 sccm per square centimeter of the substrate, the reaction temperature is maint
Embodiment 2
[0039] Nitrate solution preparation: (weight ratio is, iron nitrate: chromium nitrate: nickel nitrate: niobium nitrate = 1: 0.5: 3: 0.5. Ethanol solution concentration 10wt%), spray nitrate ethanol solution: spraying amount 0.5mg / cm 2 .
[0040] The stainless steel 309 plate is used as a CVD substrate (size: 205 mm in diameter) and suspended horizontally in a reaction furnace isolated from oxygen, and nitrogen gas is introduced at a flow rate of 0.5 sccm per square centimeter to preheat to 800 ° C, and hydrogen gas (flow rate: per square centimeter Substrate 0.5sccm) and hydrogen sulfide (flow rate: 0.005sccm per square centimeter substrate) reaction furnace, reduce nitrate for 5 minutes, maintain the gas flow; then apply 5V, 100mA, 200Hz AC current on the stainless steel plate, and at the same time press per square centimeter Substrate 0.5sccm (according to the natural gas raw material flow meter) is fed with natural gas pre-decomposed by W hot wire CVD reaction, the reaction
PUM
Property | Measurement | Unit |
---|---|---|
Thermal expansion coefficient | aaaaa | aaaaa |
Thickness | aaaaa | aaaaa |
Thickness | aaaaa | aaaaa |
Abstract
Description
Claims
Application Information
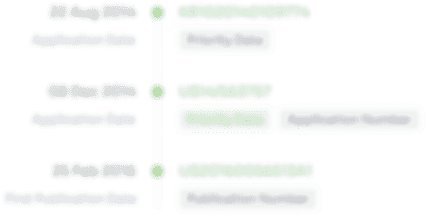
- R&D Engineer
- R&D Manager
- IP Professional
- Industry Leading Data Capabilities
- Powerful AI technology
- Patent DNA Extraction
Browse by: Latest US Patents, China's latest patents, Technical Efficacy Thesaurus, Application Domain, Technology Topic.
© 2024 PatSnap. All rights reserved.Legal|Privacy policy|Modern Slavery Act Transparency Statement|Sitemap