Synthetic leather and manufacturing method thereof
A technology of synthetic leather and manufacturing method, applied in textiles and papermaking, etc., can solve the problems of peeling, wrinkling, loss of hand feeling of synthetic leather, etc., and achieve the effect of excellent bending resistance
- Summary
- Abstract
- Description
- Claims
- Application Information
AI Technical Summary
Benefits of technology
Problems solved by technology
Method used
Image
Examples
Embodiment
[0067] Hereinafter, the present invention will be described in more detail using examples.
Synthetic example 1
[0068] [Synthesis Example 1] Synthesis of Urethane Prepolymer (A-1)
[0069] 100 parts by mass of 4,4'-diphenylmethane diisocyanate (hereinafter, abbreviated as "MDI"), 50 parts by mass of Polytetramethylene glycol (number average molecular weight: 2,000, hereinafter abbreviated as "PTMG"), 50 parts by mass of polyester polyol (6 molar adduct of propylene oxide of bisphenol A and sebacic acid The reactant, number average molecular weight: 2,000, hereinafter abbreviated as "PEs (1)") was reacted at 80° C. for 3 hours to obtain NCO%: 14.7% by mass of a urethane prepolymer.
[0070] Next, 2-hydroxyethyl acrylate (hereinafter, abbreviated as "HEA") was added and reacted at 60° C. for 2 hours to obtain an acryloyl group introduced into 15 mol % of the remaining isocyanate groups (that is, the molar ratio [isocyanate group / polymerizable unsaturated group] = 85 / 15) urethane prepolymer (A-1).
Synthetic example 2
[0071] [Synthesis Example 2] Synthesis of Urethane Prepolymer (A-2)
[0072] Add 100 mass parts of MDI, 50 mass parts of PTMG, 50 mass parts of polyester polyol (ethylene glycol and 1,4- The reactant of butanediol and sebacic acid, number average molecular weight: 2,000, hereinafter abbreviated as "PEs (2)"), was reacted at 80°C for 3 hours to obtain NCO%: 14.6% by mass of urethane pre Polymer.
[0073] Then, HEA was added and reacted at 60° C. for 2 hours to obtain an acryloyl group introduced into 15 mol % of the remaining isocyanate groups (that is, molar ratio [isocyanate group / polymerizable unsaturated group] = 85 / 15). Urethane prepolymer (A-2).
PUM
Property | Measurement | Unit |
---|---|---|
Viscosity | aaaaa | aaaaa |
Abstract
Description
Claims
Application Information
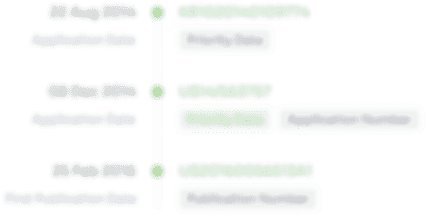
- R&D Engineer
- R&D Manager
- IP Professional
- Industry Leading Data Capabilities
- Powerful AI technology
- Patent DNA Extraction
Browse by: Latest US Patents, China's latest patents, Technical Efficacy Thesaurus, Application Domain, Technology Topic.
© 2024 PatSnap. All rights reserved.Legal|Privacy policy|Modern Slavery Act Transparency Statement|Sitemap