Welding structure for welding inner cladding and end plug of fuel rod
A technology for welding structures and fuel rods, which is used in fuel elements, greenhouse gas reduction, nuclear power generation, etc., can solve problems such as increased flow resistance, clogging of annular fuel inner flow channels, and reduced coolant inner tube flow, etc. Safety, reduce the probability of damage to fuel rods, and ensure the effect of welding quality
- Summary
- Abstract
- Description
- Claims
- Application Information
AI Technical Summary
Problems solved by technology
Method used
Image
Examples
Example Embodiment
[0020] The present invention will be further described in detail below in conjunction with the drawings and specific embodiments.
[0021] The welding structure is used for welding the inner cladding and the end plug of the annular fuel rod, and includes an inner cladding welding step 1, a mother pipe 2 and an outer cladding welding step 3, which form a hollow through-tube structure. The inner shell welding step 1, the mother pipe 2 and the outer shell welding step 3 are integrally formed. The step of the inner cladding welding step 1 is an annular protrusion along the inner diameter direction for welding with the inner cladding of the annular fuel rod. The height of the annular protrusion of the inner cladding welding step 1 is the same as the thickness of the inner cladding of the annular fuel rod; The step of the welding step 3 is an annular protrusion along the outer diameter direction for welding with the annular fuel rod outer shell, and the height of the annular protrusion of
PUM
Property | Measurement | Unit |
---|---|---|
The inside diameter of | aaaaa | aaaaa |
Abstract
Description
Claims
Application Information
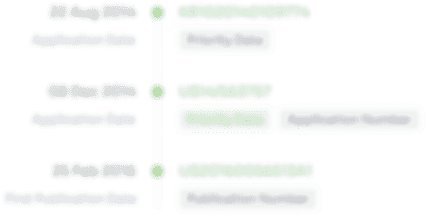
- R&D Engineer
- R&D Manager
- IP Professional
- Industry Leading Data Capabilities
- Powerful AI technology
- Patent DNA Extraction
Browse by: Latest US Patents, China's latest patents, Technical Efficacy Thesaurus, Application Domain, Technology Topic.
© 2024 PatSnap. All rights reserved.Legal|Privacy policy|Modern Slavery Act Transparency Statement|Sitemap