Core heat setting process method
A process method and heat-setting technology, applied in the direction of thin-film/thick-film capacitors, laminated capacitors, etc., can solve the problems of core metal layer oxidation, winding film hollowing phenomenon, etc., and achieve obvious effects.
- Summary
- Abstract
- Description
- Claims
- Application Information
AI Technical Summary
Benefits of technology
Problems solved by technology
Method used
Image
Examples
Embodiment 1
[0026] see figure 1 , a core heat-setting process method, comprising the following steps:
[0027] Step 1. Use a tray with a compartment to carry capacitor cores with 1 / 3 of the capacity of the oven. The capacitor cores are separated from each other, and then put into the first oven, and use a vacuum pump to pump the inside of the first oven. Vacuum treatment, keep the vacuum pressure in the box at 4-7mbar, so that the air between the winding metal film in the capacitor core can be discharged, and the bonding degree of the metal film winding can be improved;
[0028] Step 2. Raise the temperature in the first baking oven to 88-91°C and keep it warm for 3-5 hours. Within the temperature range, the surface of the metal mold begins to be pre-shaped to prepare for the subsequent heat treatment;
[0029] Step 3. Transfer the capacitor core to the second oven, dry the nitrogen, remove the moisture in the nitrogen, and then transport the nitrogen to the second oven, discharge the air
Embodiment 2
[0034] Please refer to figure 1 , a core heat-setting process method, comprising the following steps:
[0035] Step 1. Use a tray with a compartment to carry capacitor cores with 1 / 3 of the capacity of the oven. The capacitor cores are separated from each other, and then put into the first oven, and use a vacuum pump to pump the inside of the first oven. Vacuum treatment to keep the vacuum pressure in the box at 6mbar, so that the air between the winding metal films in the capacitor core can be discharged, and the bonding degree of the metal film winding can be improved;
[0036] Step 2. Raise the temperature in the first baking oven to 89°C and keep it warm for 3.5 hours. Within the temperature range, the surface of the metal mold begins to be pre-shaped to prepare for the subsequent heating and heat treatment;
[0037] Step 3. Transfer the capacitor core to the second oven, dry the nitrogen gas, remove the moisture in the nitrogen, then transport the nitrogen gas to the seco
Embodiment 3
[0042] see figure 1 , a core heat-setting process method, comprising the following steps:
[0043] Step 1. Use a tray with a compartment to carry capacitor cores with 1 / 3 of the capacity of the oven. The capacitor cores are separated from each other, and then put into the first oven, and use a vacuum pump to pump the inside of the first oven. Vacuum treatment to keep the vacuum pressure in the box at 5mbar, so that the air between the winding metal films in the capacitor core can be discharged, and the bonding degree of the metal film winding can be improved;
[0044] Step 2. Raise the temperature in the first baking oven to 90°C and keep it warm for 4 hours. Within the temperature range, the surface of the metal mold begins to be pre-shaped to prepare for the subsequent heating and heat treatment;
[0045] Step 3. Transfer the capacitor core to the second oven, dry the nitrogen gas, remove the moisture in the nitrogen, then transport the nitrogen gas to the second oven, disch
PUM
Property | Measurement | Unit |
---|---|---|
Thickness | aaaaa | aaaaa |
Thickness | aaaaa | aaaaa |
Thickness | aaaaa | aaaaa |
Abstract
Description
Claims
Application Information
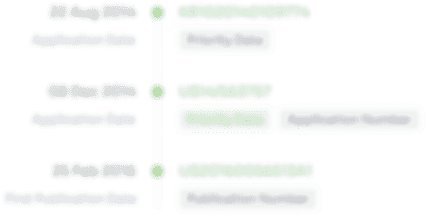
- R&D Engineer
- R&D Manager
- IP Professional
- Industry Leading Data Capabilities
- Powerful AI technology
- Patent DNA Extraction
Browse by: Latest US Patents, China's latest patents, Technical Efficacy Thesaurus, Application Domain, Technology Topic.
© 2024 PatSnap. All rights reserved.Legal|Privacy policy|Modern Slavery Act Transparency Statement|Sitemap