Composite heat-conductive material and preparation method thereof
A technology of composite heat-conducting materials and polymers, applied in textiles and papermaking, fiber treatment, carbon fiber, etc., can solve the problem of low external thermal conductivity, achieve low raw material cost, simple and easy experimental operation method, and wide application range Effect
- Summary
- Abstract
- Description
- Claims
- Application Information
AI Technical Summary
Benefits of technology
Problems solved by technology
Method used
Image
Examples
Embodiment 1
[0043] Embodiment 1 prepares carbon nanofiber / silver epoxy resin
[0044] (1) Configuration of electrospinning solution: polyacrylonitrile (M w =140000g·mol -1 ~170000g·mol -1 ) was directly dissolved in N,N-dimethylformamide, stirred vigorously at room temperature until the solution was transparent, and prepared as an electrospinning solution.
[0045] (2) The step of preparing electrospinning cloth: put the electrospinning solution in step 1 into a 10mL syringe, and spray the electrospinning through the spinning nozzle at the end of the syringe, and control the extrusion speed to 0.1mm / min by the syringe pump ~0.4mm / min; the receiver is a drum, the distance from the spinning nozzle to the receiver is 10~25cm; the positive voltage is 10~20kV, and the negative voltage is -2.0kV~-2.5kV. The obtained fibers are solidified in a drying oven at 180-300°C for 1-2 hours to obtain an electrospun cloth, and then sintered at 1000-1500°C for 1-2 hours in a tube furnace with an argo
Embodiment 2
[0052] Embodiment 2 thermal conductivity detection
[0053] Through the preparation method of Example 1 and the conditions for preparing carbon nanofibers shown in Table 2, a sample to be tested for thermal conductivity was prepared.
[0054] Table 2. Different conditions for the preparation of carbon nanofibers
[0055]
[0056] Wherein sample 1 is a comparative example, wherein the carbon nanofiber cloth of depositing silver nanoparticles is not folded, that is, it does not form a wave shape, and is directly placed in a polytetrafluoroethylene mold, adding epoxy resin polymer base, curing agent and Catalyst (its mass ratio is 1:1:0.1), put the mold into a vacuum oven for defoaming, solidify and shape in the oven, and obtain the sample to be tested. And adjust the carbon nanofiber cloth of depositing silver nanoparticles to account for the preparation mass percentage of the sample to be tested to be 0% (that is, without adding the carbon nanofiber cloth of depositing silver
Embodiment 3
[0061] Embodiment 3 prepares carbon nanofiber / silver epoxy resin
[0062] Prepared according to the method of Example 1, the only difference is that the electrochemical deposition step in step 3 is replaced by photodeposition. Specifically, the carbon nanofibers are placed in a strong acid solution (concentrated sulfuric acid, concentrated hydrochloric acid, concentrated nitric acid) for 20 minutes, subjected to surface modification treatment, and then washed and dried; the surface modified CNF is immersed in a silver nitrate solution (0.1g / L~0.5g / L), with constant magneton stirring, SXDN-150E utilizes the full-spectrum AM 1.5G solar illumination (100mW cm -2 ), the deposition time is 10min to 15min, then washed with distilled water until neutral, dried and washed in an oven; the dried CNF / Ag was sintered in a tube furnace with an argon atmosphere at low temperature (150-250°C) for 2 hours. The photodeposition method can obtain the same effect as that of the electrochem
PUM
Property | Measurement | Unit |
---|---|---|
Thermal conductivity | aaaaa | aaaaa |
Abstract
Description
Claims
Application Information
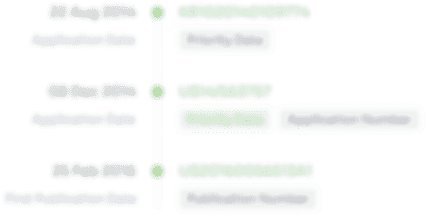
- R&D Engineer
- R&D Manager
- IP Professional
- Industry Leading Data Capabilities
- Powerful AI technology
- Patent DNA Extraction
Browse by: Latest US Patents, China's latest patents, Technical Efficacy Thesaurus, Application Domain, Technology Topic.
© 2024 PatSnap. All rights reserved.Legal|Privacy policy|Modern Slavery Act Transparency Statement|Sitemap