Friction welding method for cast super alloy and martensite stainless steel
A martensitic stainless steel and superalloy technology, applied in welding equipment, manufacturing tools, non-electric welding equipment, etc., can solve problems such as poor weldability, brittle phase precipitation, and increased alloy crack sensitivity, and achieve strong operability and process. Simple, good weld quality results
- Summary
- Abstract
- Description
- Claims
- Application Information
AI Technical Summary
Benefits of technology
Problems solved by technology
Method used
Image
Examples
Embodiment 1
[0029] The welding base material is 1Cr12Ni2WMoVNb stainless steel and K405 superalloy pipe fittings with a wall thickness of 10-15mm. The specific steps are:
[0030] Step 1: Use acetone or alcohol to clean the parts to be welded before welding to ensure that the surface is free of oil, paint, foreign debris and other pollutants.
[0031] Step 2: Clamp the cast superalloy and the martensitic stainless steel bar on the moving fixture and the rotating fixture of the friction welding machine respectively.
[0032] Step 3: Perform the first-stage friction welding with a rotating speed of 1500r / min, a friction pressure of 1MPa, and a friction time of 6s.
[0033] Step 4: After step 3, perform the second-stage friction welding with a friction pressure of 8.5MPa and a friction time of 20s.
[0034] Step 5: Immediately after the end of step 4, brake and apply a 10MPa upsetting pressure for 60s.
[0035] Step 6: Clear the internal and external flash of the weldment.
[0036] After f
Embodiment 2
[0038] The welding base material is 1Cr12Ni2WMoVNb stainless steel and K417 superalloy pipe fittings with a wall thickness of 10-15mm. The difference between the welding method and Example 1 is:
[0039] Step 4: After step 3, perform the second-stage friction welding with a friction pressure of 8.7MPa and a friction time of 21s.
[0040] Step 5: Immediately after the end of step 4, brake and apply 12MPa upsetting pressure for 60s.
[0041] After fluorescence inspection, no defects such as cracks and pores were found in the weld area, and the tensile strength of the joint was σ b It is 853MPa.
Embodiment 3
[0043] The welding parent material is 1Cr12Ni2WMoVNb stainless steel and K423 superalloy pipe fittings with a wall thickness of 10-15mm. The difference between the welding method and Example 1 is:
[0044] Step 3: Perform the first-stage friction welding with a rotating speed of 1500r / min, a friction pressure of 1MPa, and a friction time of 7s.
[0045] Step 4: After step 3, perform the second-stage friction welding with a friction pressure of 9.0MPa and a friction time of 22s.
[0046] Step 5: Immediately after the end of step 4, brake and apply 12MPa upsetting pressure for 60s.
[0047] After fluorescence inspection, no defects such as cracks and pores were found in the weld area, and the tensile strength of the joint was σ b It is 866MPa.
PUM
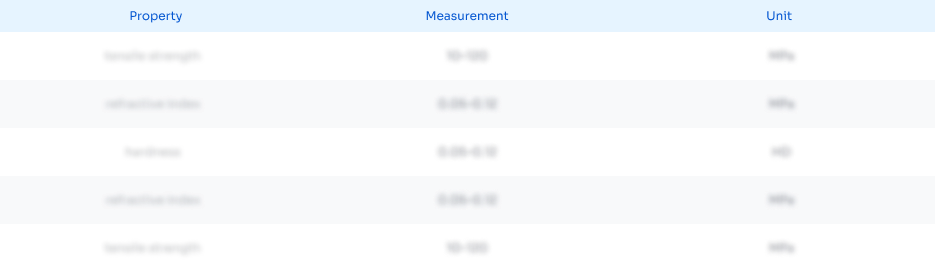
Abstract
Description
Claims
Application Information
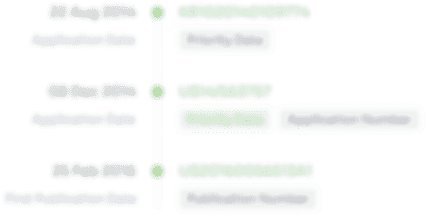
- R&D Engineer
- R&D Manager
- IP Professional
- Industry Leading Data Capabilities
- Powerful AI technology
- Patent DNA Extraction
Browse by: Latest US Patents, China's latest patents, Technical Efficacy Thesaurus, Application Domain, Technology Topic.
© 2024 PatSnap. All rights reserved.Legal|Privacy policy|Modern Slavery Act Transparency Statement|Sitemap