Continuum surface lightweight structure generation method and system based on finite element result
A generation system and surface structuring technology, applied in design optimization/simulation, image data processing, 3D modeling, etc., can solve the problems of small force, inability to obtain better calculation results, limited application scope, etc., to ensure complete sexual effect
- Summary
- Abstract
- Description
- Claims
- Application Information
AI Technical Summary
Problems solved by technology
Method used
Examples
Example Embodiment
[0043] Example 1:
[0044] figure 1 This is the flow chart of the method for generating the lightweight structure on the surface of the continuum based on the finite element results in the first embodiment of the present invention. see figure 1 , a method for generating a lightweight structure on a continuum surface based on finite element results includes:
[0045] Step 101: Obtain the curved surface design area of the product, where the product includes products such as medical protective gear, protective casing, and building curtain wall.
[0046] Step 102: Perform finite element mesh division and domain division on the surface design area to obtain a plurality of divided design blocks.
[0047] The surface design area is known, and the design area is divided into design blocks. The design blocks can be uniform size blocks or design blocks of different sizes. The size definition principle can be based on the maximum deviation of the result index of the grid calculation in
Example Embodiment
[0059] Example 2:
[0060] figure 2 This is the flow chart of the method for generating the lightweight structure on the surface of the continuum based on the finite element results in the second embodiment of the present invention. see figure 2 , the method for generating a lightweight structure on a continuum surface based on finite element results in this embodiment includes:
[0061] Step 201: Obtain the surface design area of the product.
[0062] Step 202: Perform finite element mesh division and domain division on the surface design area to obtain a plurality of divided design blocks.
[0063] Step 203: Perform finite element calculation on the design blocks, and set random points in each of the design blocks according to the calculation results, specifically including:
[0064] Random dots of different densities are arranged in each of the different design blocks.
[0065] Step 204: Perform surface structuring on each of the random points to obtain structure line
Example Embodiment
[0073] Example 3:
[0074] image 3 A system structure diagram is generated for the lightweight structure of the continuum surface based on the finite element results in Example 3 of the present invention. see image 3 , the light-weight structure generation system for the continuum surface based on the finite element results in this embodiment includes:
[0075] The first acquisition module 301 is used to acquire the curved surface design area of the product.
[0076] The division module 302 is configured to perform finite element mesh division and domain division on the surface design area to obtain a plurality of divided design blocks.
[0077] The random point setting module 303 is used for setting random points in each of the design blocks.
[0078] The structuring module 304 is configured to perform surface structuring on each of the random points to obtain structure lines.
[0079] The subdivision module 305 is configured to subdivide the structure lines by using a
PUM
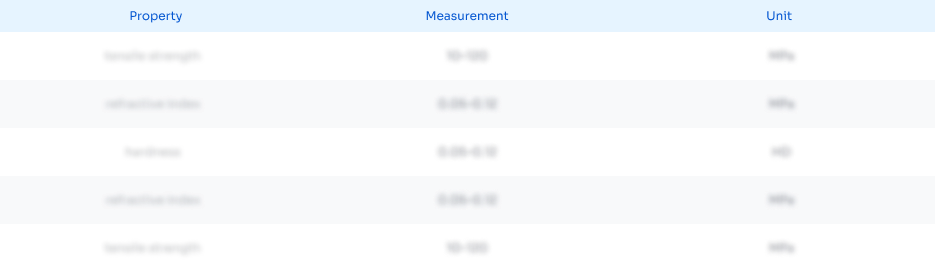
Abstract
Description
Claims
Application Information
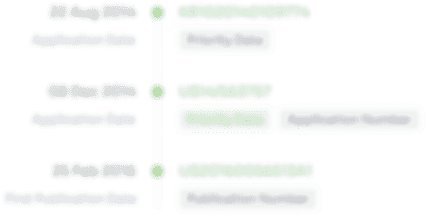
- R&D Engineer
- R&D Manager
- IP Professional
- Industry Leading Data Capabilities
- Powerful AI technology
- Patent DNA Extraction
Browse by: Latest US Patents, China's latest patents, Technical Efficacy Thesaurus, Application Domain, Technology Topic.
© 2024 PatSnap. All rights reserved.Legal|Privacy policy|Modern Slavery Act Transparency Statement|Sitemap