High-temperature-resistant high-strength aluminum alloy and preparation method thereof
An aluminum alloy, high-strength technology, applied in the field of aluminum alloy preparation, can solve problems such as poor strength and heat resistance, obstruction, etc., and achieve good strengthening effect and good comprehensive mechanical properties
- Summary
- Abstract
- Description
- Claims
- Application Information
AI Technical Summary
Problems solved by technology
Method used
Image
Examples
Embodiment 1
[0035] Step 1: Weigh Al, Mg, master alloy Al-25 Cu, master alloy Al-25 Sc, master alloy Al according to the weight percentage of 5% Cu, 2% Mg, 0.3% Sc, 0.2% Zr, and the balance is Al -10 Zr;
[0036] Step 2: sending Al, Mg, master alloy Al-Cu, master alloy Al-Sc, and master alloy Al-Zr into the preheating kettle for preheating at a temperature of 130°C;
[0037] Step 3: First put Al and Mg into the melting tank for melting operation, add after Al and Mg are completely melted, raise the temperature to 725°C, add the master alloy Al-Cu, master alloy Al-Sc, master alloy Al-Zr, until the material melts;
[0038] Step 4: After the material is melted, remove the scum on the surface and raise the temperature to 774°C;
[0039] Step 5: Cool down to 713°C, pour into a mold that has been preheated to 250°C for casting, and air-cool to room temperature to obtain the aluminum alloy;
[0040] Step 6: Put the aluminum alloy obtained in Step 5 into a heating furnace and heat it at 480°C for
Embodiment 2
[0043] Step 1: Weigh Al, Mg, master alloy Al-25 Cu, master alloy Al-25 Sc, master alloy Al according to the weight percentage of 6% Cu, 3% Mg, 0.5% Sc, 0.5% Zr, and the balance is Al -10 Zr;
[0044] Step 2: sending Al, Mg, master alloy Al-Cu, master alloy Al-Sc, and master alloy Al-Zr into the preheating kettle for preheating at a temperature of 140°C;
[0045]Step 3: First put Al and Mg into the melting tank for melting operation, add after Al and Mg are completely melted, raise the temperature to 735°C, add the master alloy Al-Cu, master alloy Al-Sc, master alloy Al-Zr, until the material melts;
[0046] Step 4: After the material is melted, remove the scum on the surface and raise the temperature to 782°C;
[0047] Step 5: Cool down to 737°C, pour into a mold that has been preheated to 250-350°C for casting, and air-cool to room temperature to obtain the aluminum alloy;
[0048] Step 6: Put the aluminum alloy obtained in step 5 into a heating furnace and heat it at 500°C f
Embodiment 3
[0051] Step 1: Weigh Al, Mg, master alloy Al-25 Cu, master alloy Al-25 Sc, master alloy Al according to the weight percentage of 5.5% Cu, 2.5% Mg, 0.4% Sc, 0.35% Zr, and the balance is Al -10 Zr;
[0052] Step 2: sending Al, Mg, master alloy Al-Cu, master alloy Al-Sc, and master alloy Al-Zr into the preheating kettle for preheating at a temperature of 135°C;
[0053] Step 3: First put Al and Mg into the melting tank for melting operation, add after Al and Mg are completely melted, raise the temperature to 730°C, add the master alloy Al-Cu, master alloy Al-Sc, master alloy Al-Zr, until the material melts;
[0054] Step 4: After the material is melted, remove the scum on the surface and raise the temperature to 778°C;
[0055] Step 5: Cool down to 725°C, pour into a mold that has been preheated to 300°C in advance for casting, and cool down to room temperature in air to obtain the aluminum alloy;
[0056] Step 6: Put the aluminum alloy obtained in Step 5 into a heating furnace a
PUM
Property | Measurement | Unit |
---|---|---|
Tensile strength | aaaaa | aaaaa |
Tensile strength | aaaaa | aaaaa |
Tensile strength | aaaaa | aaaaa |
Abstract
Description
Claims
Application Information
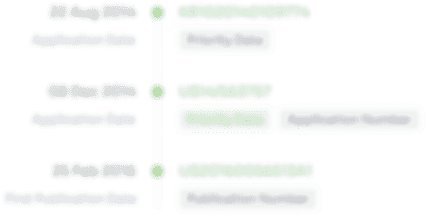
- R&D Engineer
- R&D Manager
- IP Professional
- Industry Leading Data Capabilities
- Powerful AI technology
- Patent DNA Extraction
Browse by: Latest US Patents, China's latest patents, Technical Efficacy Thesaurus, Application Domain, Technology Topic.
© 2024 PatSnap. All rights reserved.Legal|Privacy policy|Modern Slavery Act Transparency Statement|Sitemap