Lead-zinc oxide ore recycling and harmless treatment system and method
A harmless treatment and lead-zinc oxide technology, which is applied in waste heat treatment, energy efficiency improvement, lighting and heating equipment, etc., can solve the problems of restricting the resource utilization of lead-zinc oxide, high energy consumption of smelting equipment, complex treatment process, etc., to achieve Improve processing capacity and heat utilization rate, reduce production cost, and strengthen the effect of metallurgical reaction process
- Summary
- Abstract
- Description
- Claims
- Application Information
AI Technical Summary
Problems solved by technology
Method used
Image
Examples
Embodiment 1
[0036] A kind of lead-zinc oxide resource harmless treatment system, such as figure 1 As shown, the treatment system includes: a preheating unit 1 , a precalciner 2 , a rotary kiln 3 and a cooling machine 4 .
[0037] The preheating unit 1 is connected with the precalcining furnace 2. In the preheating unit 1, the lead-zinc oxide material is directly or indirectly contacted with the zinc oxide flue gas from the precalcining furnace 2, and the preheating of the lead-zinc oxide material is completed. Unit 1 can use any gas-solid heat exchange equipment that can realize direct or indirect contact heat exchange between zinc oxide dust and lead-zinc oxide materials, such as: cyclone preheating unit, multi-hearth furnace preheating unit and the inner layer is a material channel, and the outer layer is a material channel. The layer is the casing heat exchange equipment such as the flue gas channel, etc. In the preheating unit 1, the preheating of the lead-zinc oxide material is realize
Embodiment 2
[0046] A lead-zinc oxide ore recycling and harmless treatment system, the preheating unit is a cyclone preheating unit, and the rest are the same as in Embodiment 1. Such as figure 2 As shown, the treatment system includes: cyclone preheating unit 1, precalciner 2, rotary kiln 3 and cooler 4. Cyclone preheating unit 1 is composed of 5-stage cyclone dust collectors connected by pipelines (as attached figure 2 As shown, C1 represents the first-stage cyclone dust collector, C2 represents the second-stage cyclone dust collector, and so on). The lead-zinc oxide ore is added from the connecting pipe between the first-stage cyclone dust collector C1 and the second-stage cyclone dust collector C2 of the preheating unit. The lead-zinc oxide ore directly contacts the flue gas in the cyclone dust collector and the pipe to exchange heat, and the flue gas The waste heat in the furnace is recovered, and the lead-zinc oxide ore is preheated to 600°C-900°C. The flue gas outlet of the precal
Embodiment 3
[0067] Embodiment 3: (Cyclone preheating unit preheating)
[0068] A lead-zinc oxide ore recycling harmless treatment method, the specific steps are as follows:
[0069](1) The composition of 50000t raw materials is Pb 2.26% Zn 9.73% CaO 21.86% SiO 2 28.34%Al 2 o 3 0.35% MgO 0.57% S 4.34% (lead, zinc oxidation rate up to 60%) low-grade lead-zinc oxide ore is crushed and ball milled in sequence. After crushing, the particle size ≤ 25mm accounts for 70%; the material is ball milled to a particle size ≤ 60μm, and the moisture content is ≤ 0.8%.
[0070] (2) Divide 10,000t of anthracite coal with a carbon content of 60%, 2mm≤particle size≤6mm, and moisture≤8% into two parts, of which 5000t is ball-milled, with powdered coal particle size≤60μm and moisture≤0.6%; the other 5000t is prepared as 2mm≤ Granular coal with a particle size of ≤8mm and a moisture content of ≤10% is stockpiled for future use.
[0071] (3) A production system with a processing capacity of 3000t / d is adop
PUM
Property | Measurement | Unit |
---|---|---|
Granularity | aaaaa | aaaaa |
Granularity | aaaaa | aaaaa |
Abstract
Description
Claims
Application Information
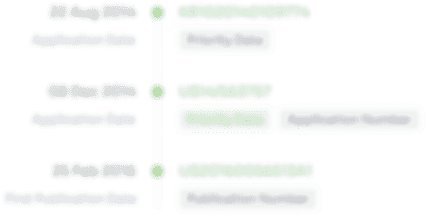
- R&D Engineer
- R&D Manager
- IP Professional
- Industry Leading Data Capabilities
- Powerful AI technology
- Patent DNA Extraction
Browse by: Latest US Patents, China's latest patents, Technical Efficacy Thesaurus, Application Domain, Technology Topic.
© 2024 PatSnap. All rights reserved.Legal|Privacy policy|Modern Slavery Act Transparency Statement|Sitemap