Cutting fluid regeneration device
A regeneration device and cutting fluid technology, which is applied in liquid separation, grease/oily substance/floating matter removal device, biological water/sewage treatment, etc., can solve the problem of large consumption, short service life of cutting fluid, heavy odor at the production site, etc. problems, to achieve the effects of reducing emissions, saving waste liquid disposal costs, and reducing defective and scrap rates
- Summary
- Abstract
- Description
- Claims
- Application Information
AI Technical Summary
Benefits of technology
Problems solved by technology
Method used
Image
Examples
Embodiment Construction
[0022] In order to make the technical solutions of the present invention clearer and clearer to those skilled in the art, the present invention will be further described in detail below in conjunction with the embodiments and accompanying drawings.
[0023] figure 1 A preferred implementation form of the cutting fluid device is shown, including a regeneration tank 1 and a floating oil recovery device 2 . The floating oil recovery device 2 is located at the upper end of the regeneration box 1 outside. The regeneration tank 1 is provided with a settling tank 3 , a separation tank 4 and a liquid storage tank 5 sequentially from left to right. The upper part of the settling tank 3 is connected with the floating oil recovery device 2 , the inlet end of the settling tank 3 is connected with the sewage pipe, and the outlet end of the settling tank 3 is connected with the inlet end of the separation tank 4 through the first self-priming pump 7 . The outlet end of the separation tank 4
PUM
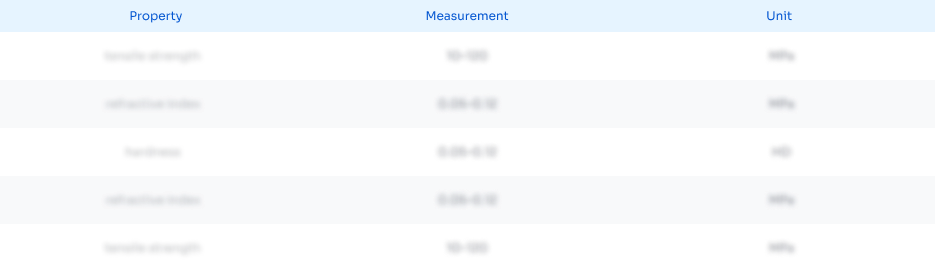
Abstract
Description
Claims
Application Information
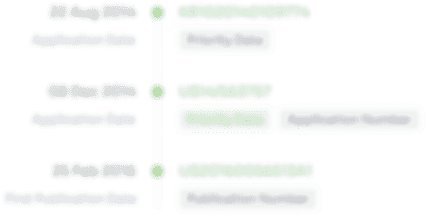
- R&D Engineer
- R&D Manager
- IP Professional
- Industry Leading Data Capabilities
- Powerful AI technology
- Patent DNA Extraction
Browse by: Latest US Patents, China's latest patents, Technical Efficacy Thesaurus, Application Domain, Technology Topic.
© 2024 PatSnap. All rights reserved.Legal|Privacy policy|Modern Slavery Act Transparency Statement|Sitemap