Manipulator positioning method for polishing spatial curved surface of optical element
A technology for optical components and positioning methods, which is applied to optical surface grinders, grinding/polishing equipment, and parts of grinding machine tools. It can solve problems such as complex curve structures and inability to complete the polishing of optical components in space, and improve polishing efficiency. , precise positioning and high processing precision
- Summary
- Abstract
- Description
- Claims
- Application Information
AI Technical Summary
Problems solved by technology
Method used
Examples
Example Embodiment
[0041] The present invention will be further described in detail below in conjunction with the accompanying drawings and embodiments. It should be understood that the specific embodiments described here are only used to explain related inventions, rather than to limit the invention. It should also be noted that, for ease of description, only parts related to the invention are shown in the accompanying drawings.
[0042] It should be noted that, in the case of no conflict, the embodiments of the present invention and the features in the embodiments can be combined with each other. The present invention will be described in detail below with reference to the accompanying drawings and examples.
[0043] figure 1 It shows the process flow of the manipulator positioning method for polishing the space curved surface of the optical element provided by the embodiment of the present invention. like figure 1 Shown, described manipulator positioning method, comprises the steps:
[0044
PUM
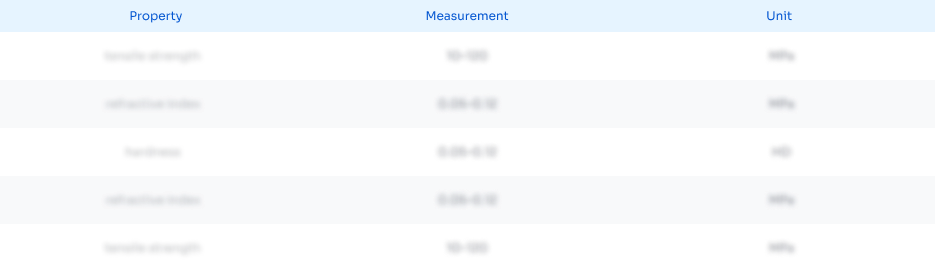
Abstract
Description
Claims
Application Information
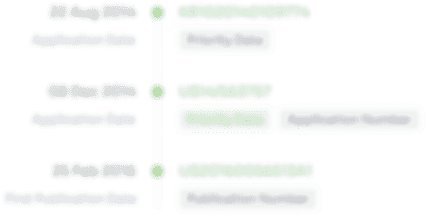
- R&D Engineer
- R&D Manager
- IP Professional
- Industry Leading Data Capabilities
- Powerful AI technology
- Patent DNA Extraction
Browse by: Latest US Patents, China's latest patents, Technical Efficacy Thesaurus, Application Domain, Technology Topic.
© 2024 PatSnap. All rights reserved.Legal|Privacy policy|Modern Slavery Act Transparency Statement|Sitemap