Preparation method of galvanizing solution for metal workpieces
A technology of metal workpiece and galvanizing bath, applied in metal material coating process, hot-dip plating process, coating and other directions, can solve the problems of limited improvement of galvanizing quality of metal workpiece and general performance of galvanizing bath, and achieve excellent Corrosion resistance, excellent performance, improved protection effect
- Summary
- Abstract
- Description
- Claims
- Application Information
AI Technical Summary
Benefits of technology
Problems solved by technology
Method used
Examples
preparation example Construction
[0017] A method for preparing a galvanizing solution for metal workpieces, comprising the following steps:
[0018] (1) Mix aluminum block and zinc block together, heat to melt, and then stir at 500r / min for 40min to obtain a mixture;
[0019] (2) Add aluminum-zirconium master alloy and aluminum-lanthanum master alloy to the above mixed solution, heat until it melts, and then stir to obtain a galvanizing solution.
[0020] As a further technical solution: the mass ratio of the aluminum block to the zinc block is 1:45-50.
[0021] As a further technical solution: the heating and melting temperature is 620°C.
[0022] As a further technical solution: the mass ratio of the aluminum-zirconium master alloy, the aluminum-lanthanum master alloy, and the mixed solution is 1:0.02:80.
[0023] As a further technical solution: the mass fraction of zirconium in the aluminum-zirconium master alloy is 30%.
[0024] As a further technical solution: the mass fraction of lanthanum in the alu
Embodiment 1
[0028] A method for preparing a galvanizing solution for metal workpieces, comprising the following steps:
[0029] (1) Mix aluminum block and zinc block together, heat to melt, and then stir at 500r / min for 40min to obtain a mixture;
[0030] (2) Add aluminum-zirconium master alloy and aluminum-lanthanum master alloy to the above mixed solution, heat until it melts, and then stir to obtain a galvanizing solution.
[0031] As a further technical solution: the mass ratio of the aluminum block to the zinc block is 1:45.
[0032] As a further technical solution: the heating and melting temperature is 620°C.
[0033] As a further technical solution: the mass ratio of the aluminum-zirconium master alloy, the aluminum-lanthanum master alloy, and the mixed solution is 1:0.02:80.
[0034] As a further technical solution: the mass fraction of zirconium in the aluminum-zirconium master alloy is 30%.
[0035] As a further technical solution: the mass fraction of lanthanum in the alumin
Embodiment 2
[0038] A method for preparing a galvanizing solution for metal workpieces, comprising the following steps:
[0039] (1) Mix aluminum block and zinc block together, heat to melt, and then stir at 500r / min for 40min to obtain a mixture;
[0040] (2) Add aluminum-zirconium master alloy and aluminum-lanthanum master alloy to the above mixed solution, heat until it melts, and then stir to obtain a galvanizing solution.
[0041] As a further technical solution: the mass ratio of the aluminum block to the zinc block is 1:50.
[0042] As a further technical solution: the heating and melting temperature is 620°C.
[0043] As a further technical solution: the mass ratio of the aluminum-zirconium master alloy, the aluminum-lanthanum master alloy, and the mixed solution is 1:0.02:80.
[0044] As a further technical solution: the mass fraction of zirconium in the aluminum-zirconium master alloy is 30%.
[0045] As a further technical solution: the mass fraction of lanthanum in the alumin
PUM
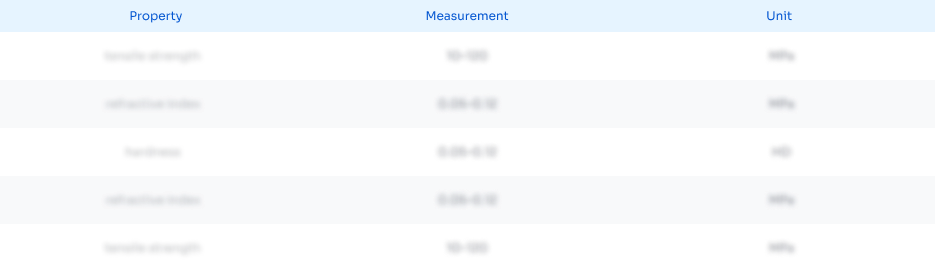
Abstract
Description
Claims
Application Information
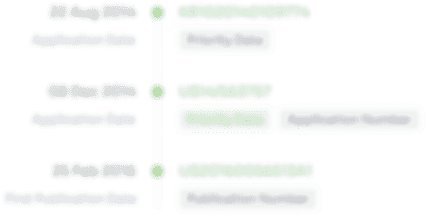
- R&D Engineer
- R&D Manager
- IP Professional
- Industry Leading Data Capabilities
- Powerful AI technology
- Patent DNA Extraction
Browse by: Latest US Patents, China's latest patents, Technical Efficacy Thesaurus, Application Domain, Technology Topic.
© 2024 PatSnap. All rights reserved.Legal|Privacy policy|Modern Slavery Act Transparency Statement|Sitemap