Solvent-free waterborne polyurethane capable of being continuously produced and preparation method of solvent-free waterborne polyurethane
A water-based polyurethane and solvent-free technology, applied in the field of water-based polyurethane, can solve the problems of poor compatibility between resin and cationic materials, negative impact on consumers and the environment, and inability to realize continuous production, so as to achieve continuous automatic production, save equipment investment, The effect of saving organic solvent resources
- Summary
- Abstract
- Description
- Claims
- Application Information
AI Technical Summary
Problems solved by technology
Method used
Examples
Example Embodiment
[0044]Example 1
[0045]Step 1: accurate weighing
[0046]92 parts of isophorone diisocyanate;
[0047]300 parts of polytetrahydrofuran glycol (number average molecular weight is 2000);
[0048]1.5 parts neopentyl glycol;
[0049]38 parts of Ymer-N120 non-ionic hydrophilic glycol of Perstorp Group;
[0050]750 parts of deionized water;
[0051]Step 2: Add polytetrahydrofuran diol and Perstorp’s Ymer-N120 non-ionic hydrophilic diol into the reaction kettle and vacuum dehydration at 120°C for 1 hour;
[0052]Step 3: Cool the reactor to 70°C, add isophorone diisocyanate at a stirring speed of 300r / min, control the temperature to 80°C, and react for 2h;
[0053]Step 4: Add neopentyl glycol to the reaction kettle, control the temperature at 80°C, and react for 2 hours;
[0054]Step 5: Add 10 parts of emulsifier DNS-18 to the reaction kettle, control the temperature at 60°C, and react for 0.5h;
[0055]Step 6: Pass the prepolymer and deionized water through a static mixer, then through a high-gravity dispersion reactor, a
Example Embodiment
[0056]Example 2
[0057]Step 1: accurate weighing
[0058]215 parts of dicyclohexylmethane diisocyanate;
[0059]205 parts of polytetrahydrofuran diol (number average molecular weight is 1000);
[0060]100 parts polypropylene glycol (number average molecular weight is 2000);
[0061]2 parts of 1,4-butanediol;
[0062]46 parts of Ymer-N120 non-ionic hydrophilic glycol of Perstorp Group;
[0063]792 parts of deionized water;
[0064]Step 2: Add polytetrahydrofuran diol, polypropylene glycol and Perstorp’s Ymer-N120 non-ionic hydrophilic diol into the reaction kettle and vacuum dehydration at 120°C for 1.5 hours;
[0065]Step 3: Cool the reactor to 70°C, add dicyclohexylmethane diisocyanate at a stirring speed of 300r / min, control the temperature to 85°C, and react for 2h;
[0066]Step 4: Add 1,4-butanediol to the reaction kettle, control the temperature at 80°C, and react for 2 hours;
[0067]Step 5: Add 20 parts of emulsifier DNS-500 to the reaction kettle, control the temperature at 60°C, and react for 2 hours;
[0068
Example Embodiment
[0069]Example 3
[0070]Step 1: accurate weighing
[0071]115 parts of toluene diisocyanate;
[0072]210 parts of polytetrahydrofuran glycol (number average molecular weight is 2000);
[0073]100 parts of polybutylene adipate diol (number average molecular weight is 1000);
[0074]2 parts of 1,6-hexanediol;
[0075]42 parts of Ymer-N120 non-ionic hydrophilic glycol of Perstorp Group;
[0076]945 parts of deionized water;
[0077]Step 2: Add polytetrahydrofuran diol, polybutylene adipate diol and Perstorp’s Ymer-N120 non-ionic hydrophilic diol into the reaction kettle and vacuum dehydration at 120°C for 1 hour;
[0078]Step 3: Cool the reactor to 50°C, add toluene diisocyanate at a stirring speed of 300r / min, control the temperature to 70°C, and react for 2h;
[0079]Step 4: Add 1,4-butanediol to the reaction kettle, control the temperature at 85°C, and react for 2.5 hours;
[0080]Step 5: Add dimethylethanolamine to the reaction kettle, control the temperature at 40°C, and react for 0.5h;
[0081]Step 6: Pass the prepo
PUM
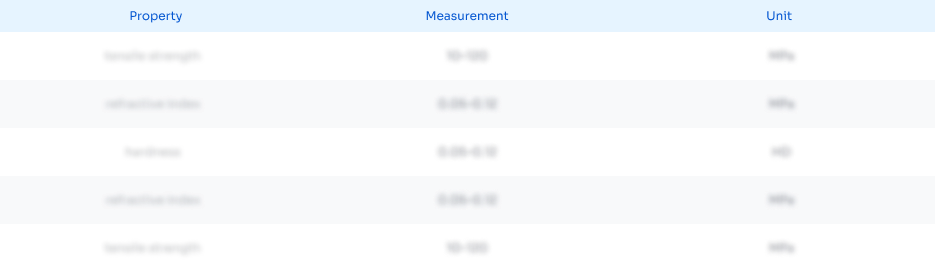
Abstract
Description
Claims
Application Information
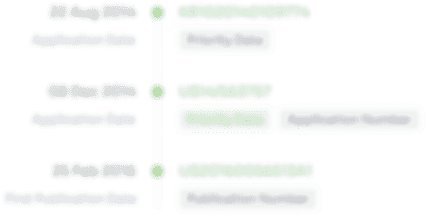
- R&D Engineer
- R&D Manager
- IP Professional
- Industry Leading Data Capabilities
- Powerful AI technology
- Patent DNA Extraction
Browse by: Latest US Patents, China's latest patents, Technical Efficacy Thesaurus, Application Domain, Technology Topic.
© 2024 PatSnap. All rights reserved.Legal|Privacy policy|Modern Slavery Act Transparency Statement|Sitemap