Manufacturing process of ultra-large low-temperature liquid-filled insulating layer
A manufacturing process and insulating layer technology, which is applied in the field of ultra-large low-temperature liquid-filled insulating layer manufacturing process, can solve the problems of easy cracking of insulation and affecting the service life of liquid tanks, etc., to improve toughness and strength, reduce cracking risk, and simple manufacturing process Effect
- Summary
- Abstract
- Description
- Claims
- Application Information
AI Technical Summary
Problems solved by technology
Method used
Image
Examples
Example Embodiment
[0023] Example 1:
[0024] The present invention provides the following technical solution: an ultra-large cryogenic hydraulic irrigation insulating process, including the following steps:
[0025] A, first cleaning the surface of the tank;
[0026] B, then sprayed in the surface of the tank;
[0027] C, sprayed the first layer of foam;
[0028] D, after the first layer of glass is installed on the first layer foam;
[0029] E, then spray the second layer of foam outside the glass layer;
[0030] F, after the air gel / rock cotton is installed;
[0031] G, spray the third layer of foam;
[0032] H, install the second floor glass network outside the third foam;
[0033] I, spray the fourth layer of foam outside the outer glass network;
[0034] J, finally sprayed polyurea outside the fourth layer of foam to complete the insulating layer.
[0035] In the present embodiment, the first layer of foam, the second layer foam, the third layer foam, the fourth layer foam content component a
Example Embodiment
[0041] Example 2:
[0042] Ultra-large low temperature hydraulic irrigation insulating process, including the following steps:
[0043] A, first cleaning the surface of the tank;
[0044] B, then sprayed in the surface of the tank;
[0045] C, sprayed the first layer of foam;
[0046] D, after the first layer of glass is installed on the first layer foam;
[0047] E, then spray the second layer of foam outside the glass layer;
[0048] F, after the air gel / rock cotton is installed;
[0049] G, spray the third layer of foam;
[0050] H, install the second floor glass network outside the third foam;
[0051] I, spray the fourth layer of foam outside the outer glass network;
[0052] J, finally sprayed polyurea outside the fourth layer of foam to complete the insulating layer.
[0053] In the present embodiment, the first layer foam, the second layer foam, the third layer foam, the fourth layer foam content component is composed, and the components include 40 parts by weight of the
Example Embodiment
[0059] Example 3:
[0060] Ultra-large low temperature hydraulic irrigation insulating process, including the following steps:
[0061] A, first cleaning the surface of the tank;
[0062] B, then sprayed in the surface of the tank;
[0063] C, sprayed the first layer of foam;
[0064] D, after the first layer of glass is installed on the first layer foam;
[0065] E, then spray the second layer of foam outside the glass layer;
[0066] F, after the air gel / rock cotton is installed;
[0067] G, spray the third layer of foam;
[0068] H, install the second floor glass network outside the third foam;
[0069] I, spray the fourth layer of foam outside the outer glass network;
[0070] J, finally sprayed polyurea outside the fourth layer of foam to complete the insulating layer.
[0071] In the present embodiment, the first layer foam, the second layer foam, the third layer foam, the fourth layer foam content component are completed, and the components comprise 32 parts of the rebound
PUM
Property | Measurement | Unit |
---|---|---|
Thickness | aaaaa | aaaaa |
Thickness | aaaaa | aaaaa |
Thickness | aaaaa | aaaaa |
Abstract
Description
Claims
Application Information
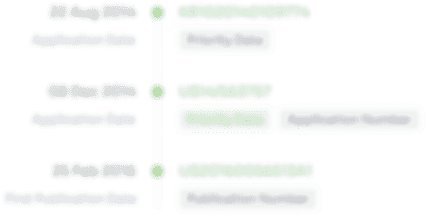
- R&D Engineer
- R&D Manager
- IP Professional
- Industry Leading Data Capabilities
- Powerful AI technology
- Patent DNA Extraction
Browse by: Latest US Patents, China's latest patents, Technical Efficacy Thesaurus, Application Domain, Technology Topic.
© 2024 PatSnap. All rights reserved.Legal|Privacy policy|Modern Slavery Act Transparency Statement|Sitemap