Glass slurry for automobile compression molding front windshield and preparation method thereof
A front windshield, glass paste technology, applied in the coating and other directions, can solve the problems of insufficient acid and alkali resistance, poor anti-stickiness, etc., and achieves a suitable expansion coefficient range, simple preparation process, excellent acid resistance and resistance. The effect of stickiness
- Summary
- Abstract
- Description
- Claims
- Application Information
AI Technical Summary
Problems solved by technology
Method used
Image
Examples
Embodiment 1
[0059] Preparation of glass powder: weigh Bi 2o 3 : 56.7 parts; SiO 2 : 34.0 copies; B 2 o 3 : 3.1 parts; ZnO: 1.6 parts; ZrO 2 : 0 parts; TiO 2 : 0.3 parts; Al 2 o 3 : 0.2 parts; Fe 2 o 3 : 0.2 parts; NaF: 0.2 parts; MgO: 0 parts; CaO: 0.1 parts; 2 O: 1.6 copies; K 2 O: 0.1 parts; Na 2 O: Add 2.0 parts of glass powder raw materials into the mixer and mix evenly, put the uniformly mixed glass powder raw materials into a crucible, put the crucible with glass powder raw materials in a high-temperature furnace, and melt at a temperature of 1000°C 2 hours to melt the material into a uniformly mixed liquid, quickly pour the melted mixed liquid into distilled water to form glass slag; dry and crush the glass slag, put it in a ball mill with a rotation speed of 200r / min for 2 hours, and then put it into a drying box drying at 200°C, and then sieved to obtain glass powder with an average particle size of 2 μm;
[0060] Preparation of slurry: 75 parts of glass powder obtain
Embodiment 2
[0062] Preparation of glass powder: weigh Bi 2 o 3 : 57.0 parts; SiO 2 : 34.2 copies; B 2 o 3 : 3.1 parts; ZnO: 1.6 parts; ZrO 2 : 0 parts; TiO 2 : 0.3 parts; Al 2 o 3 : 0 copies; Fe 2 o 3 : 0 parts; NaF: 0.2 parts; MgO: 0 parts; CaO: 0 parts; 2 O: 1.6 copies; K 2 O: 0 parts; Na 2 O: Add 2.0 parts of glass powder raw materials into the mixer and mix evenly, put the uniformly mixed glass powder raw materials into a crucible, put the crucible with glass powder raw materials in a high-temperature furnace, and melt at a temperature of 1000°C 2 hours to melt the material into a uniformly mixed liquid, quickly pour the melted mixed liquid into distilled water to form glass slag; dry and crush the glass slag, put it in a ball mill with a rotation speed of 200r / min for 2 hours, and then put it into a drying box drying at 200°C, and then sieved to obtain glass powder with an average particle size of 2 μm;
[0063] Preparation of slurry: 75 parts of glass powder obtained in
Embodiment 3
[0065] Preparation of glass powder: weigh Bi 2 o 3 : 55.8 parts; SiO 2 : 30.3 copies; B 2 o 3 : 3.0 parts; ZnO: 1.6 parts; ZrO 2 : 0.7 parts; TiO 2 : 4.0 parts; Al 2 o 3 : 0 copies; Fe 2 o 3 : 0 parts; NaF: 0.5 parts; MgO: 0 parts; CaO: 0 parts; 2 O: 1.8 copies; K 2 O: 0.4 parts; Na 2 O: Add 2.0 parts of glass powder raw materials into the mixer and mix evenly, put the uniformly mixed glass powder raw materials into a crucible, put the crucible with glass powder raw materials in a high-temperature furnace, and melt at a temperature of 1000°C 2 hours to melt the material into a uniformly mixed liquid, quickly pour the melted mixed liquid into distilled water to form glass slag; dry and crush the glass slag, put it in a ball mill with a rotation speed of 200r / min for 2 hours, and then put it into a drying box drying at 200°C, and then sieved to obtain glass powder with an average particle size of 2 μm;
[0066] Preparation of slurry: 70 parts of glass powder obtained
PUM
Property | Measurement | Unit |
---|---|---|
Particle size | aaaaa | aaaaa |
Abstract
Description
Claims
Application Information
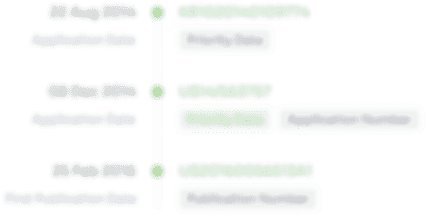
- R&D Engineer
- R&D Manager
- IP Professional
- Industry Leading Data Capabilities
- Powerful AI technology
- Patent DNA Extraction
Browse by: Latest US Patents, China's latest patents, Technical Efficacy Thesaurus, Application Domain, Technology Topic.
© 2024 PatSnap. All rights reserved.Legal|Privacy policy|Modern Slavery Act Transparency Statement|Sitemap