Spiral conveyor with auxiliary blades and spiral discharging sedimentation centrifuge
A technology of screw conveyor and auxiliary blade, applied in the field of solid-liquid separation, can solve the problems of low solid content in light phase and poor separation effect, and achieve the effect of low cost, increased area, and improved separation factor Fr
- Summary
- Abstract
- Description
- Claims
- Application Information
AI Technical Summary
Problems solved by technology
Method used
Image
Examples
Example Embodiment
[0029]Example 1:
[0030]Such asimage 3 ,Figure 4 As shown, the helical conveyor of the sub-blades of the present invention is between the screw blades 6 of the conventional conventional helical conveyor, which increases several sub-blades 10, and the width of the sub-blades 10 is less than the joint of the spiral blade 6. At the distance, the adjacent two sub-blades 10 are staggered, and the original continuously complete helical channel space between the spiral blades 6 is further separated into a zone flow channel 15, thereby extending the separation path length of the suspension and effectively improves the separation effect.
[0031]In this embodiment, the sub-blades 10 are planar straight blades, along the radial direction of the screw conveyor, and soldered the inner cylindrical 4 outer circumference, one side welding on the spiral blade 6, ie The left edge of a portion of the sub-blades 10 in each helical space is fixed to the left spiral blade 6, and the first gap 13 is left at the
Example Embodiment
[0035]Example 2:
[0036]Such asFigure 5 As shown in the present embodiment, the planar straight blade in the first embodiment is changed to a curved blade, and the sub-blade 10 has a certain bending curvature, and the curved outer convex direction of the curved surface is coincided with the direction of rotation of the drum, that is, the elongation particles in the suspension. Will move along the outer convex surface of the curved blade, such settings can effectively increase the centrifugal force, so that the weight phase particles are easily settled.
Example Embodiment
[0037]Example 3:
[0038]Such asFigure 6 ,Figure 7 As shown, the present embodiment deflects an angle setting of the secondary blade 10 in the first embodiment in the first embodiment.Figure 7 The angle α of the inverse blades 10 and the axis of the drum is 45 degrees, preferably 5 to 30 degrees, adjacent blades parallel, and the deflection direction is consistent. In this embodiment, the sub-bladder 10 is disposed in the rear screw passage of the discharge hole 3, and the transport resistance of the drum cone 11 drying zone can be reduced, and the discharge of the solid phase material can be reduced.
PUM
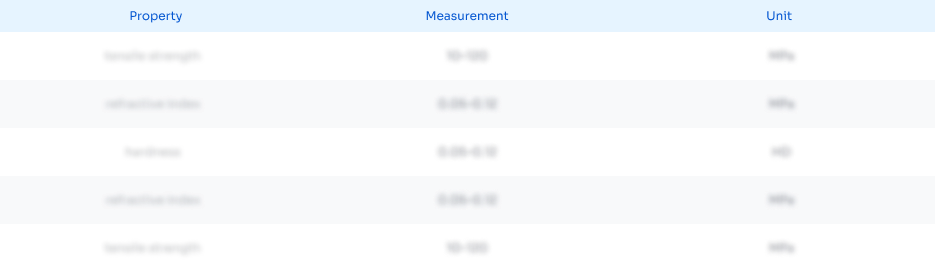
Abstract
Description
Claims
Application Information
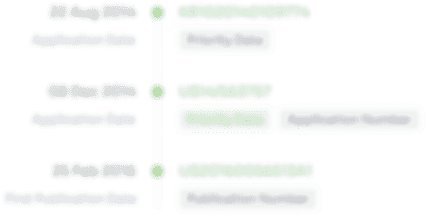
- R&D Engineer
- R&D Manager
- IP Professional
- Industry Leading Data Capabilities
- Powerful AI technology
- Patent DNA Extraction
Browse by: Latest US Patents, China's latest patents, Technical Efficacy Thesaurus, Application Domain, Technology Topic.
© 2024 PatSnap. All rights reserved.Legal|Privacy policy|Modern Slavery Act Transparency Statement|Sitemap