Clamping device for fusion welding of automobile part
An auto parts, fusion welding technology, applied in auxiliary devices, welding equipment, auxiliary welding equipment and other directions, can solve the problems of unsatisfactory fixing effect, low work efficiency, and inability to adjust the fixed angle of welding parts, so as to improve work efficiency and improve work efficiency. Welding accuracy, the effect of wide applicability
- Summary
- Abstract
- Description
- Claims
- Application Information
AI Technical Summary
Benefits of technology
Problems solved by technology
Method used
Image
Examples
Embodiment
[0032] see Figure 1-9 , the present invention provides a technical solution: a clamping device for fusion welding of auto parts, including a clamping mechanism 1, a carrying mechanism 3 and a controller 4, and the clamping mechanism 1 includes a first support plate 101, a first motor 102 , first hinge arm 103, second motor 104, second hinge arm 105, third motor 106, third hinge arm 107, fourth motor 108, storage table 109, servo motor 1103, bevel worm gear 1104, three bevel worms 1105, three lead screws 1106, three sliders 1107 and three asynchronous motors 2, the inside of the first brace 101 is connected with the first motor 102 by screws, the upper surface of the first brace 101 is connected with the first hinge arm The lower surface of 103 is welded, the front surface of the first hinge arm 103 is connected with the second motor 104 by screws, the output shaft of the second motor 104 is welded with the inner side wall of the second hinge arm 105, and the inner side wall of t
PUM
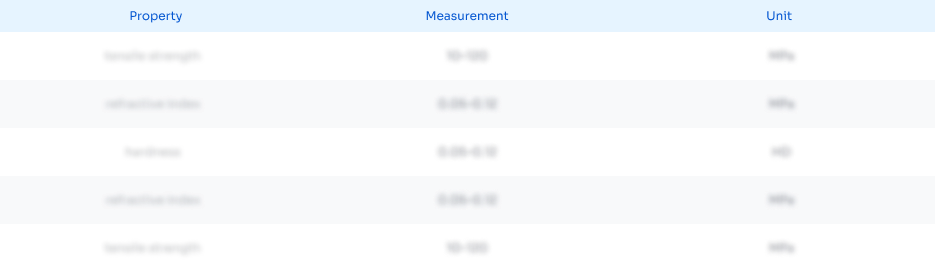
Abstract
Description
Claims
Application Information
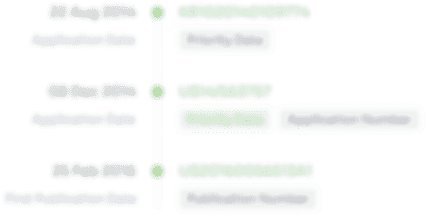
- R&D Engineer
- R&D Manager
- IP Professional
- Industry Leading Data Capabilities
- Powerful AI technology
- Patent DNA Extraction
Browse by: Latest US Patents, China's latest patents, Technical Efficacy Thesaurus, Application Domain, Technology Topic.
© 2024 PatSnap. All rights reserved.Legal|Privacy policy|Modern Slavery Act Transparency Statement|Sitemap