High-ductility concrete as well as preparation method and equipment thereof
A technology for high ductility concrete and mixtures, applied in clay preparation devices, chemical instruments and methods, cement mixing devices, etc., can solve the problem of polyvinyl alcohol fiber breakage, reduce the mechanical properties of high ductility concrete materials, and affect the use range of high ductility concrete, etc. problems, to achieve great economic value, enhance synergies, and broaden the scope of use
- Summary
- Abstract
- Description
- Claims
- Application Information
AI Technical Summary
Problems solved by technology
Method used
Image
Examples
Embodiment 1
[0056] A kind of high ductility concrete, the parts by weight of each material are with reference to table 2, comprise the following steps:
[0057] Step 1: Add cement, quartz sand, fly ash, coarse aggregate, fine aggregate, polyvinyl alcohol fiber and coumarone resin to the mixer for mixing according to the mass, at a speed of 190r / min, stir for 7min, and heat to 90°C, mix evenly to obtain the first mixture;
[0058] Step 2: Add the water reducer and water to the first mixture of the mixer according to the mass, and mix at a speed of 360r / min, stir for 30s, and mix evenly to obtain the second mixture;
[0059] Step 3: Add permanganate to the second mixture according to the mass, rotate at 180r / min, stir for 1min, mix well, and heat to 85°C to obtain the third mixture;
[0060] Step 4: Use a mixer to continue stirring the third mixture at a speed of 80 r / min, and stir for 2 hours to obtain high ductility concrete.
Embodiment 2
[0062] Step 1: Add cement, quartz sand, fly ash, coarse aggregate, fine aggregate, polyvinyl alcohol fiber and coumarone resin to the mixer for mixing according to the mass, at a speed of 190r / min, stir for 5min, and heat to 80°C, mix evenly to obtain the first mixture;
[0063] Step 2: Add the water reducer and water into the mixer according to the mass and mix them at a speed of 360r / min, stir for 20s, and mix evenly to obtain the second mixture;
[0064] Step 3: Add permanganate to the second mixture according to the mass, rotate at a speed of 180r / min, stir for 2min, mix well, and heat to 110°C to obtain the third mixture;
[0065] Step 4: Use a mixer to continue stirring the third mixture at a speed of 80 r / min, and stir for 1 hour to obtain high ductility concrete.
Embodiment 3
[0067] Step 1: Add cement, quartz sand, fly ash, coarse aggregate, fine aggregate, polyvinyl alcohol fiber and coumarone resin to the mixer for mixing according to the mass, at a speed of 190r / min, stir for 6.5min, and heat to 88°C, mix evenly to obtain the first mixture;
[0068] Step 2: Add the water reducer and water into the mixer according to the mass and mix them at a speed of 360r / min, stir for 25s, and mix evenly to obtain the second mixture;
[0069] Step 3: Add permanganate to the second mixture according to the mass, rotate at 180r / min, stir for 1.5min, mix well, and heat to 95°C to obtain the third mixture;
[0070] Step 4: Use a mixer to continue stirring the third mixture at a speed of 80 r / min, and stir for 1.5 hours to obtain high ductility concrete.
[0071] In Examples 1-3, the particle size range of the coarse aggregate is 6.5-7.5mm, 8.5-12.5mm and 9.5-10.5mm.
[0072] In Examples 1-3, the particle size range of the fine aggregate is 0.5-2mm, 1.4-2.4m
PUM
Property | Measurement | Unit |
---|---|---|
Particle size | aaaaa | aaaaa |
Particle size | aaaaa | aaaaa |
Viscosity | aaaaa | aaaaa |
Abstract
Description
Claims
Application Information
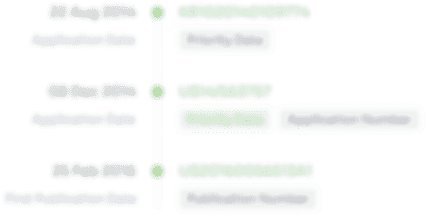
- R&D Engineer
- R&D Manager
- IP Professional
- Industry Leading Data Capabilities
- Powerful AI technology
- Patent DNA Extraction
Browse by: Latest US Patents, China's latest patents, Technical Efficacy Thesaurus, Application Domain, Technology Topic.
© 2024 PatSnap. All rights reserved.Legal|Privacy policy|Modern Slavery Act Transparency Statement|Sitemap