Amide hydrodeoxygenation method
A technology of hydrodeoxygenation and amide, applied in chemical instruments and methods, metal/metal oxide/metal hydroxide catalysts, preparation of organic compounds, etc., can solve problems such as few reports, and achieve simple and controllable reaction process. , excellent catalytic performance, the effect of improving catalytic activity
- Summary
- Abstract
- Description
- Claims
- Application Information
AI Technical Summary
Benefits of technology
Problems solved by technology
Method used
Image
Examples
Embodiment 1
[0036] Catalyst preparation:
[0037] Mix and dissolve 118.5g of copper nitrate trihydrate, 54.8g of zinc nitrate hexahydrate, 2.5g of ammonium molybdate tetrahydrate, 89.1g of magnesium nitrate hexahydrate, and 220.7g of aluminum nitrate nonahydrate with equal amounts of water. Add 20% sodium carbonate solution dropwise to the above mixture at 30°C until the pH is 8.9, stir for 1 hour after the addition, filter, wash until the sodium ion is less than 500ppm, dry at 120°C, and roast at 500°C. The catalyst is designated CAT-1.
[0038] reaction:
[0039] Tablet the catalyst CAT-1 and sieve it into 20-40 mesh particles. Take 4g of the catalyst and fill it in the middle section of the fixed bed reaction tube. Fill the two ends of the reaction tube with inert quartz sand. The reaction is carried out under the conditions of ℃ and reaction pressure of 3.0Mpa, and the mass space velocity of the raw material 2-pyrrolidone is 0.4h -1 , the solvent is tetrahydrofuran, the mass ratio of
Embodiment 2
[0041] Catalyst preparation: same as embodiment 1.
[0042] reaction:
[0043] After the catalyst CAT-1 was pressed into tablets, it was sieved into 20-40 mesh particles, and 4g of the catalyst was loaded into the middle section of the fixed-bed reaction tube, and inert quartz sand was filled at both ends of the reaction tube. The reaction is carried out under the conditions of ℃ and reaction pressure of 2.0Mpa, and the mass space velocity of the raw material 2-pyrrolidone is 0.4h -1 , the solvent is tetrahydrofuran, the mass ratio of solvent to 2-pyrrolidone is 1:1, and the molar ratio of hydrogen to 2-pyrrolidone is 30:1. After the reaction was carried out for 48 hours, samples were taken and analyzed by gas chromatography. During the reaction, the conversion rate of 2-pyrrolidone was 93.3%, and the selectivity of the product tetrahydropyrrole was 96.5%.
Embodiment 3
[0045] Catalyst preparation:
[0046] Mix and dissolve 88.1g of copper nitrate trihydrate, 54.8g of zinc nitrate hexahydrate, 2.5g of ammonium molybdate tetrahydrate, 89.1g of magnesium nitrate hexahydrate, and 294.3g of aluminum nitrate nonahydrate with equal amounts of water. Add 20% sodium carbonate solution dropwise to the above mixture at 30°C until the pH is 9.0, stir for 1 hour after the addition, filter, wash until the sodium ion is less than 500ppm, dry at 120°C, and roast at 500°C. The catalyst is designated CAT-3.
[0047] reaction:
[0048] The reaction process is the same as in Example 1, and the catalyst is CAT-3. After the reaction was carried out for 48 hours, samples were taken and analyzed by gas chromatography. During the reaction, the conversion rate of 2-pyrrolidone was 96.8%, and the selectivity of the product tetrahydropyrrole was 92.8%.
PUM
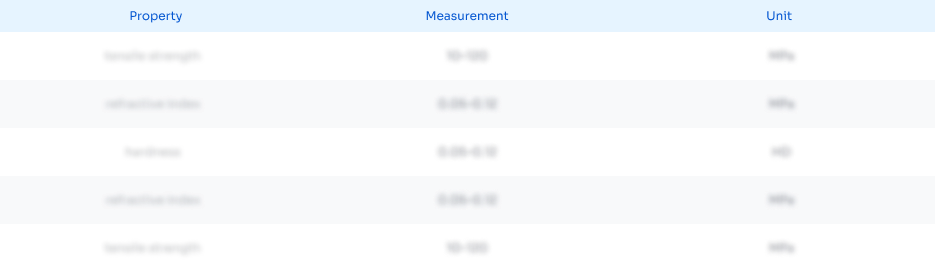
Abstract
Description
Claims
Application Information
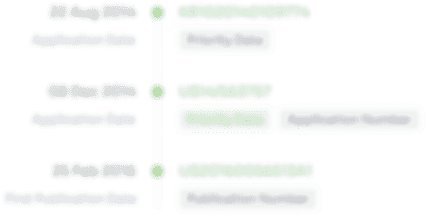
- R&D Engineer
- R&D Manager
- IP Professional
- Industry Leading Data Capabilities
- Powerful AI technology
- Patent DNA Extraction
Browse by: Latest US Patents, China's latest patents, Technical Efficacy Thesaurus, Application Domain, Technology Topic.
© 2024 PatSnap. All rights reserved.Legal|Privacy policy|Modern Slavery Act Transparency Statement|Sitemap