Rotor three-in-one combined pressing die
A three-in-one, rotor technology, applied in the manufacture of stator/rotor body, metal processing, metal processing equipment, etc., can solve the problem that the insulating end plates on the lower insulating end plate are separated from each other, reduce the forming effect of the motor rotor, and reduce the machining accuracy of the motor rotor and other problems, to achieve the effect of reducing the number of pressing, optimizing the overall structure and pressing method, and reducing the number of driving parts
- Summary
- Abstract
- Description
- Claims
- Application Information
AI Technical Summary
Problems solved by technology
Method used
Examples
Example Embodiment
[0029] The present invention will be made in conjunction with the accompanying drawings and examples, but is not discussed as limiting the invention.
[0030] Embodiment. Triangular combined stamper in the rotor, constitute figure 1 As shown, the mounting seat 1 is slidably connected to the fixing seat 1, and the upper surface of the pallet 2 is slidably connected to the pallet 2, and the pallet 2 and the upper press plate 3 are slid so late along the vertical direction. The outer side of the upper platen 3 is connected to the drive rod, and the middle portion of the upper pressure plate 3 is provided with a block 4, and a placement table 6 connecting the fixing seat 1 is provided below.
[0031] The placing table 6 is provided with a first step 601 having a connecting commutator, and a plug-in block 60 having a fastening connection switching device is provided on the placing table 6 on the top of the first step 601. The commutator is built. The upper surface of the first step 601 is
PUM
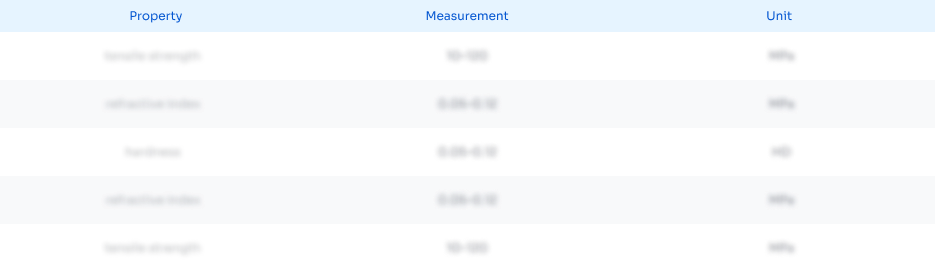
Abstract
Description
Claims
Application Information
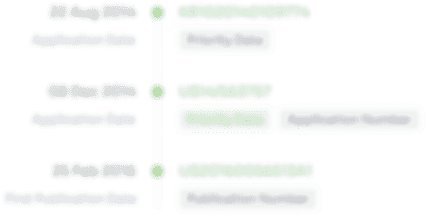
- R&D Engineer
- R&D Manager
- IP Professional
- Industry Leading Data Capabilities
- Powerful AI technology
- Patent DNA Extraction
Browse by: Latest US Patents, China's latest patents, Technical Efficacy Thesaurus, Application Domain, Technology Topic.
© 2024 PatSnap. All rights reserved.Legal|Privacy policy|Modern Slavery Act Transparency Statement|Sitemap