Spraying method of corrosion-resistant coating for top of crude oil distillation tower
A technology of corrosion-resistant coatings and crude oil distillation, which is applied to coatings, devices for coating liquid on surfaces, and pre-treated surfaces, etc., can solve the problems of short protection time, affecting production and income, and achieve the goal of improving the effective time of corrosion resistance Effect
- Summary
- Abstract
- Description
- Claims
- Application Information
AI Technical Summary
Problems solved by technology
Method used
Image
Examples
Embodiment 1
[0030] The present embodiment adopts the corrosion-resistant coating and the spraying method in the specific implementation mode, specifically as follows:
[0031] Adopt the ni of 70 parts by weight, the mo of 28 parts by weight, the remaining components (i.e. 1 part by weight cr and 1 part by weight fe) of 2 parts by weight are raw materials to form corrosion-resistant coating; And carry out spraying by following steps, step 1, distillation Sandblasting on the inner surface of the tower: use white corundum with a particle size greater than or equal to 35 mesh, sandblasting pressure: 0.7Mpa, sandblasting angle: 75 degrees, sandblasting distance: 135mm; when the surface roughness reaches RA10, sandblasting stops;
[0032] Step 2, mixing and proportioning raw materials: prepare raw materials according to the proportion, then put them into a pulverizer for pulverization, control the pulverized particle size after pulverization is 30um, complete pulverization, add epoxy resin after pu
Embodiment 2
[0038] The difference between this embodiment and Example 1 is that the ni of 65 parts by weight, the mo of 27 parts by weight, and the remaining components of 8 parts by weight are raw materials to form a corrosion-resistant coating (wherein 3 parts by weight of cr, 3 parts by weight of fe and 2 parts by weight of the remaining components);
[0039] Step 1, sandblasting pressure: 0.5Mpa Sandblasting angle: 80 degrees, sandblasting distance: 120mm; when the surface roughness reaches RA8, sandblasting stops;
[0040] In step 2: the crushed particle size is 5um;
[0041] In step 3: the air inlet pressure of the spray gun is 0.2Mpa, and the feeding speed of the powder coating is 120ml / min;
[0042] In step 4: the moving speed is 20cm / s, and the spraying distance is 3cm;
[0043] Step 5: Heating for the first time, the heater is 15cm away from the coating surface, energized for heating, the heating time is 20min, and the temperature is 120°C; reheating, the heating distance is
Embodiment 3
[0046] The difference between this embodiment and Example 1 is that 66 parts by weight of ni, 32 parts by weight of mo, and 2 parts by weight of the remaining components (i.e. 1 part by weight of cr and 1 part by weight of fe) are used as raw materials to form a corrosion-resistant coating;
[0047] Step 1, sandblasting pressure: 0.9Mpa Sandblasting angle: 70 degrees, sandblasting distance: 150mm; when the surface roughness reaches RA12, sandblasting stops;
[0048] In step 2: the crushed particle size is 100um;
[0049] In step 3: the air inlet pressure of the spray gun is 0.6Mpa, and the feeding speed of the powder coating is 80ml / min;
[0050] In step 4: the moving speed is 30cm / s, and the spraying distance is 2cm;
[0051] Step 5: Heating for the first time, the heater is 35cm away from the coating surface, energized for heating, the heating time is 40min, and the temperature is 80°C; reheating, the heating distance is adjusted to be 15cm from the coating surface, the he
PUM
Property | Measurement | Unit |
---|---|---|
Particle size | aaaaa | aaaaa |
Particle size | aaaaa | aaaaa |
Abstract
Description
Claims
Application Information
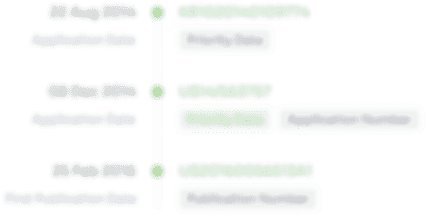
- R&D Engineer
- R&D Manager
- IP Professional
- Industry Leading Data Capabilities
- Powerful AI technology
- Patent DNA Extraction
Browse by: Latest US Patents, China's latest patents, Technical Efficacy Thesaurus, Application Domain, Technology Topic.
© 2024 PatSnap. All rights reserved.Legal|Privacy policy|Modern Slavery Act Transparency Statement|Sitemap