Welding process for one-time brazing forming of parts with different heat capacities
A welding process and component technology, applied in the field of welding process, can solve the problems of flow, incomplete penetration of solder, melting, etc., to achieve the effect of simple production operation and beautiful welding seam
- Summary
- Abstract
- Description
- Claims
- Application Information
AI Technical Summary
Problems solved by technology
Method used
Examples
Example Embodiment
[0043] Example 1
[0044] A welding process of a two-kind heat capacity component primary brazing, including the following steps:
[0045] S1, surface treatment:
[0046] The welding portion of the thin wall member 1 and the high heat capacity metal base 2 sequentially serves as a golden phase sandpaper, pickled and cleaned to remove oil, oxidation, and residual metal powder particles; free silver-based solder 3 with gold-phase sandpaper. The oxide layer, then ultrasonic cleaning, the ultrasonic frequency is 300 kHz, the ultrasonic power is 800W, and the time of ultrasonic cleaning is 10mim;
[0047] Among them, the material of the thin-walled member 1 is a can which is 4J29; the thin-walled member 1 is a thin-walled tube having a diameter of 50 mm;
[0048] The material of the high heat capacity metal base 2 is an oxygen-free copper TU00;
[0049] Silver-based solder 3 is AGCU 28 series wire, silver-based solder 3 is: Cu 26 wt%, Ni0.8 wt%, GE 1 wt%, CO 2 wt%, the margin is Ag, and t
Example Embodiment
[0067] Example 2
[0068] A welding process of a two-kind heat capacity component primary brazing, including the following steps:
[0069] S1, surface treatment:
[0070] The welding portion of the thin wall member 1 and the high heat capacity metal base 2 sequentially serves as a golden phase sandpaper, pickled and cleaned to remove oil, oxidation, and residual metal powder particles; free silver-based solder 3 with gold-phase sandpaper. The oxide layer, then ultrasound cleaning, the ultrasonic frequency is 400 kHz, the ultrasonic power is 1500W, and the time of ultrasonic cleaning is 25mim;
[0071] Among them, the material of the thin-walled member 1 is stainless steel; the thin wall member 1 is a thin-walled tube having a diameter of 100 mm;
[0072] The material of the high heat capacity metal base 2 is an oxygen-free copper Tu0;
[0073] Silver-based solder 3 is AGCU 28 series wire, silver-based solder 3 is: Cu 27 wt%, Ni0.8 wt%, GE 2WT%, CO 4WT%, margin is Ag;
[0074] S2, sol
Example Embodiment
[0091] Example 3
[0092] A welding process of a two-kind heat capacity component primary brazing, including the following steps:
[0093] S1, surface treatment:
[0094] The welding portion of the thin wall member 1 and the high heat capacity metal base 2 sequentially serves as a gold-phase sandpaper, pickled and cleaned to remove oil, oxidation, and residual metal powder particles, nickel plating, plating on the thin wall member 1. The nickel layer has a thickness of 8 μm; the oxide layer on the silver-based solder 3 is removed with a metallographic sandpaper, then ultrasonic cleaning, the ultrasonic frequency is 200 kHz, the ultrasonic power is 400W, and the time of ultrasonic cleaning is 5mim;
[0095] Among them, the material of the thin-walled member 1 is a can which is 4J29; the thin-walled member 1 is a thin-walled tube having a diameter of 20 mm;
[0096] The material of the high heat capacity metal base 2 is an oxygen-free copper TU00;
[0097] Silver-based solder 3 is the
PUM
Property | Measurement | Unit |
---|---|---|
Diameter | aaaaa | aaaaa |
Diameter | aaaaa | aaaaa |
Diameter | aaaaa | aaaaa |
Abstract
Description
Claims
Application Information
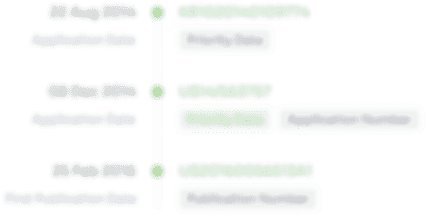
- R&D Engineer
- R&D Manager
- IP Professional
- Industry Leading Data Capabilities
- Powerful AI technology
- Patent DNA Extraction
Browse by: Latest US Patents, China's latest patents, Technical Efficacy Thesaurus, Application Domain, Technology Topic.
© 2024 PatSnap. All rights reserved.Legal|Privacy policy|Modern Slavery Act Transparency Statement|Sitemap