Aluminum magnesium containing alloy materials
A lithium-magnesium alloy and alloy technology, applied in the field of lithium-magnesium alloy materials, can solve the problems of few β single-phase alloy research reports, no commercial alloy data, poor thermal stability, etc., and achieve good plasticity, low density, high ratio the effect of strength
- Summary
- Abstract
- Description
- Claims
- Application Information
AI Technical Summary
Problems solved by technology
Method used
Examples
Example Embodiment
[0015] The above-mentioned components are prepared using the following preparation methods to prepare lithium-containing magnesium alloy materials, and the steps are as follows:
[0016] (1) Take out the alloy elements according to the proportioning scale;
[0017] (2) Smelting alloys by smelting methods;
[0018] (3) Pouring into ingots in a protective atmosphere;
[0019] (4) Peel the ingot;
[0020] (5) Carry out the homogenization treatment of the stripped ingot at 350℃±10℃ / 24h;
[0021] (6) Homogenize the ingot after homogenization treatment at 430℃±10℃ / 48h;
[0022] (7) The processed ingot is deformed into a product at room temperature or 250°C±5°C.
[0023] The performance test is performed on the lithium-containing magnesium alloy material prepared by the above method, and the test is carried out with a gold image microscope, MTS material mechanical property testing machine, and one-tenths balance equipment, and the tensile strength of the lithium-containing magnesium all
Example Embodiment
[0025] Example 1: To prepare 100 kilograms of lithium-containing magnesium alloy materials according to the following ratio, the elements to be taken out are:
[0026] Lithium (Li) 15 kg, aluminum (Al) 5 kg, zinc (Zn) 1 kg, zirconium (Zr) 0.80 kg, rare earth element rhenium (Re) 1.2 kg and the balance magnesium (Mg).
[0027] The preparation method includes smelting the weighed elements at a melting temperature of 680°C, and pouring them into an ingot under an argon atmosphere. The ingot is stripped with a machine tool and an acid solution to obtain a clean surface. The ingots are homogenized at 350℃±10℃ / 24h, and the homogenized ingots are then homogenized at 430℃±10℃ / 48h. The homogenized ingots are at room temperature or 250 Under the condition of ℃±5℃, it can be processed into products after forging or rolling deformation.
[0028] The product was kept at a temperature of 250°C for 4 hours and then taken out. It can meet the general performance requirements. HV-10A small load V
Example Embodiment
[0029] Example 2: To prepare 100 kilograms of lithium-containing magnesium alloy materials according to the following ratio, the elements to be taken out are:
[0030] 10 kg of lithium (Li), 4.5 kg of aluminum (Al), 1 kg of zinc (Zn), 0.80 kg of zirconium (Zr), 1.2 kg of rare earth element rhenium (Re) and the balance of magnesium (Mg).
[0031] The preparation method includes smelting the elements weighed out above at a smelting temperature of 720°C, and smelting them in SF 6 The ingot is poured into an ingot under the protective environment of mixed gas, and the ingot is stripped with a machine tool and acid solution to obtain a clean surface, and the stripped ingot is subjected to a homogenization treatment at 350℃±10℃ / 24h. After homogenization treatment The ingot is homogenized at 430℃±10℃ / 48h, and the homogenized ingot is processed into products by forging or rolling deformation at room temperature or 250℃±5℃.
[0032] The product was kept at a temperature of 250°C for 4 hou
PUM
Property | Measurement | Unit |
---|---|---|
Tensile strength | aaaaa | aaaaa |
Yield strength | aaaaa | aaaaa |
Tensile strength | aaaaa | aaaaa |
Abstract
Description
Claims
Application Information
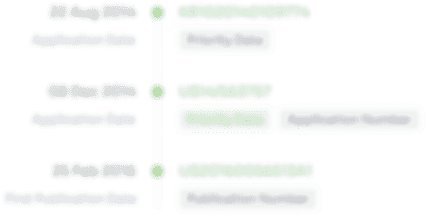
- R&D Engineer
- R&D Manager
- IP Professional
- Industry Leading Data Capabilities
- Powerful AI technology
- Patent DNA Extraction
Browse by: Latest US Patents, China's latest patents, Technical Efficacy Thesaurus, Application Domain, Technology Topic.
© 2024 PatSnap. All rights reserved.Legal|Privacy policy|Modern Slavery Act Transparency Statement|Sitemap