Yield strength 1100MPa level engineering machinery non-quenched and tempered hot rolled strip and preparation method thereof
A yield strength, engineering machinery technology, applied in the metallurgical field, can solve the problem of high production cost, achieve the effect of improving welding performance, reducing production cost and good plasticity
- Summary
- Abstract
- Description
- Claims
- Application Information
AI Technical Summary
Problems solved by technology
Method used
Examples
Example Embodiment
[0023] Example 1
[0024] The molten steel is smelted in a 150-ton converter according to the set composition and continuously cast into a slab. The set composition is C 0.06% by weight, Si 0.20%, Mn 1.60%, Nb 0.02%, V 0.04%, Ti 0.15% , Ni 0.4%, Mo 0.20%, P<0.012%, S<0.01%, the balance is iron Fe, the thickness of the cast slab is 220mm.
[0025] The cast slab is heated to 1250°C for rough rolling. The rough rolling process is 5 passes, the roughing start-rolling temperature is 1170°C, the roughing final rolling temperature is 1070°C, and an intermediate slab with a thickness of 38mm is obtained.
[0026] The intermediate billet is finished rolling, the finishing rolling process is 7 passes, the finishing rolling temperature is 980℃, the second rolling temperature is 950℃, the third rolling temperature is 930℃, the fourth rolling temperature is 890℃, and the fifth rolling temperature is 850℃. ℃, the six-rolling temperature is 820℃, the final rolling temperature is 800℃, the reduction o
Example Embodiment
[0028] Example 2
[0029] The preparation method and composition of the cast slab are the same as in Example 1, and the thickness of the cast slab is 250 mm.
[0030] The rough rolling process was the same as in Example 1, and an intermediate billet with a thickness of 58 mm was obtained.
[0031] The intermediate billet is finished rolling. The finishing rolling process is 6 passes. The finishing rolling temperature is 950°C, the second rolling temperature is 930°C, the third rolling temperature is 910°C, the fourth rolling temperature is 880°C, and the fifth rolling temperature is 850°C. ℃, the final rolling temperature is 830℃, the reduction of each pass of finishing rolling is controlled at 15-40%, and the thickness of the strip after finishing rolling is 6mm.
[0032] After finishing rolling, it is water-cooled to 400°C at a speed of 35°C / s, and then coiled by a coiler. The composition obtained by weight percentage is C 0.06%, Si 0.20%, Mn 1.60%, Nb 0.02%, V 0.04%, Ti 0.15 %, Ni
Example Embodiment
[0033] Example 3
[0034] The preparation method and composition of the cast slab are the same as in Example 1, and the thickness of the cast slab is 240 mm.
[0035] The rough rolling process was the same as in Example 1, and an intermediate billet with a thickness of 45 mm was obtained.
[0036] The intermediate billet is finished rolling, the finishing rolling process is 5 passes, the finishing rolling temperature is 1020℃, the second rolling temperature is 980℃, the third rolling temperature is 920℃, the fourth rolling temperature is 900℃, and the final rolling temperature is 880 ℃, the reduction of each pass of finishing rolling is controlled at 15-40%, and the thickness of the strip after finishing rolling is 4mm.
[0037] After finishing rolling, it is water-cooled to 200°C at a speed of 15°C / s, and then coiled by a coiler. The composition obtained by weight percentage is C 0.06%, Si 0.20%, Mn 1.60%, Nb 0.02%, V 0.04%, Ti 0.15 %, Ni 0.4%, Mo 0.20%, P<0.012%, S<0.01%, the balanc
PUM
Property | Measurement | Unit |
---|---|---|
Yield strength | aaaaa | aaaaa |
Tensile strength | aaaaa | aaaaa |
Thickness | aaaaa | aaaaa |
Abstract
Description
Claims
Application Information
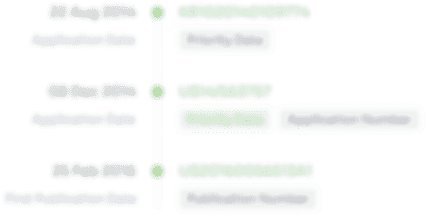
- R&D Engineer
- R&D Manager
- IP Professional
- Industry Leading Data Capabilities
- Powerful AI technology
- Patent DNA Extraction
Browse by: Latest US Patents, China's latest patents, Technical Efficacy Thesaurus, Application Domain, Technology Topic.
© 2024 PatSnap. All rights reserved.Legal|Privacy policy|Modern Slavery Act Transparency Statement|Sitemap