Quartz type pressure sensor, and production method therefor
A pressure sensor, quartz technology, applied in the direction of fluid pressure measurement using capacitance change, etc., to achieve the effect of increasing production, small changes over time, and improving processing accuracy
- Summary
- Abstract
- Description
- Claims
- Application Information
AI Technical Summary
Benefits of technology
Problems solved by technology
Method used
Image
Examples
Embodiment Construction
[0062] Embodiments of the present invention shown in the drawings will be described in detail below.
[0063] figure 1 (a) and 1(b) are vertical sectional views showing the overall structure of the contact mode capacitive pressure sensor according to an embodiment of the present invention, and figure 1 (a) A sectional view taken along the line A-A shown.
[0064] A contact mode capacitance type pressure sensor (hereinafter referred to as "pressure sensor" or "contact mode type pressure sensor") 1 is accommodated in a container 20 made of an insulating material such as ceramics. The ceramic container 20 generally includes a bottom plate 21, four side walls 22 erected from the periphery of the bottom plate 21, and an upper cover 23 fixed to the upper opening formed by the side walls 22 and provided with a vent hole 23a.
[0065] Since the side wall 22 and the upper cover 23 are not necessary, a structure in which the detection sheet 10 and the like are assembled on the bottom p
PUM
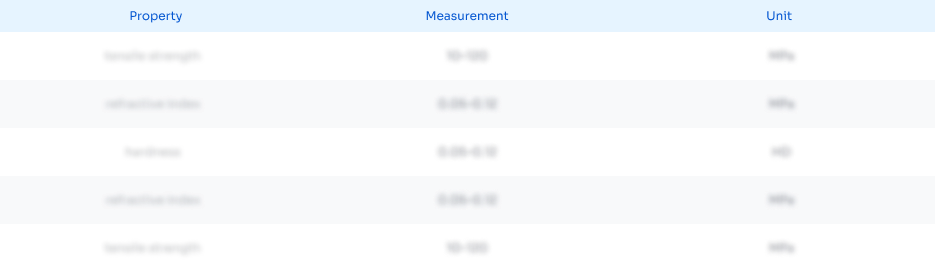
Abstract
Description
Claims
Application Information
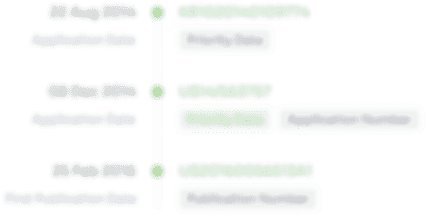
- R&D Engineer
- R&D Manager
- IP Professional
- Industry Leading Data Capabilities
- Powerful AI technology
- Patent DNA Extraction
Browse by: Latest US Patents, China's latest patents, Technical Efficacy Thesaurus, Application Domain, Technology Topic.
© 2024 PatSnap. All rights reserved.Legal|Privacy policy|Modern Slavery Act Transparency Statement|Sitemap