Axial-mode linear wind-trubine
- Summary
- Abstract
- Description
- Claims
- Application Information
AI Technical Summary
Problems solved by technology
Method used
Image
Examples
Embodiment Construction
[0022] Before we go into great detail of the preferred embodiments, we should consider some of the physical properties involved which govern the operation of this type of turbine kite system. At this time it is sufficient to understand the general design for the turbine kite from FIG. 2. This system consists of three airfoil kites 50 in tandem which are attached to the Ground Station 30 by support lines 60L and 60R, and control lines 58L and 58R (collectively the support lines and control lines will be referred to throughout this patent as control lines). By controlling the differential length of these control lines, the airfoil's direction and speed can be controlled from the ground to follow the shown Flight Path. The control lines are also directly connected to a shaft and pulley system (see FIG. 12) in the Ground Station 30. As the Airfoil Kites 50 are propelled by the wind at very high speed, all four control lines are reeled-out under tremendous force causing the pulley and shaft
PUM
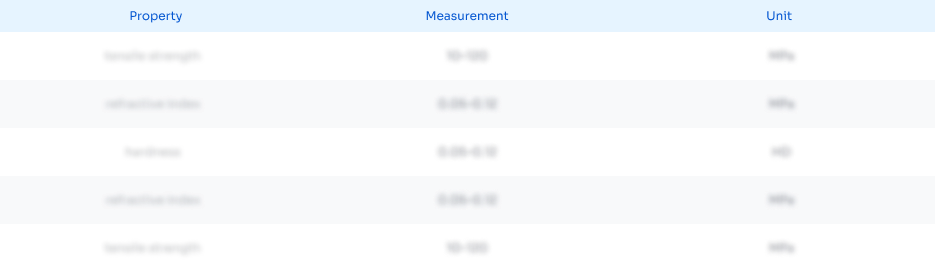
Abstract
Description
Claims
Application Information
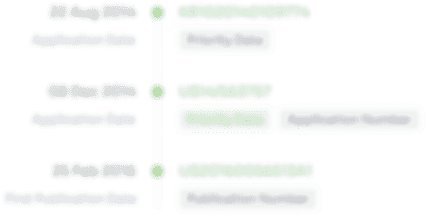
- R&D Engineer
- R&D Manager
- IP Professional
- Industry Leading Data Capabilities
- Powerful AI technology
- Patent DNA Extraction
Browse by: Latest US Patents, China's latest patents, Technical Efficacy Thesaurus, Application Domain, Technology Topic.
© 2024 PatSnap. All rights reserved.Legal|Privacy policy|Modern Slavery Act Transparency Statement|Sitemap