Travel Control Method For Self-Propelled Carriage
- Summary
- Abstract
- Description
- Claims
- Application Information
AI Technical Summary
Benefits of technology
Problems solved by technology
Method used
Image
Examples
Example
[0023]The embodiments of the present invention are now described below with reference to the accompanying drawings.
[0024]In FIGS. 1 and 2, a carriage is oriented so that F is a forward direction, Re is a backward direction, R is a rightward direction, and L is a leftward direction; and a carriage 10 is assumed to be in forward movement when working in the forward direction, and in backward movement when working in the backward direction.
[0025]FIG. 1 is a side view of a self-propelled carriage according to the present invention, comprising a caster wheel. The main elements constituting the self-propelled carriage 10 are a platform 11 that doubles as a frame for the carriage; a drive section 13 for driving the carriage 10, with the drive section 13 provided with a drive wheel 12, and mounted to a lower surface of the platform 11; and a caster wheel 15 for supporting the carriage 10, with the caster wheel 15 mounted as a reinforcing wheel 14 to a front and rear of the drive section 13.
[00
PUM
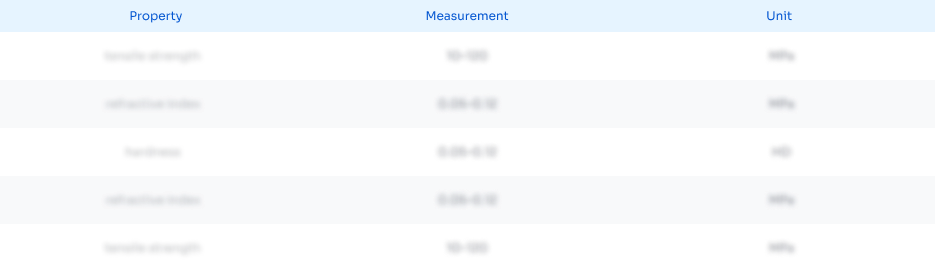
Abstract
Description
Claims
Application Information
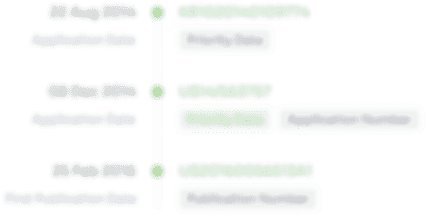
- R&D Engineer
- R&D Manager
- IP Professional
- Industry Leading Data Capabilities
- Powerful AI technology
- Patent DNA Extraction
Browse by: Latest US Patents, China's latest patents, Technical Efficacy Thesaurus, Application Domain, Technology Topic.
© 2024 PatSnap. All rights reserved.Legal|Privacy policy|Modern Slavery Act Transparency Statement|Sitemap