Gas spring with guide
a technology of gas springs and guides, applied in the direction of springs/dampers, shock absorbers, liquid based dampers, etc., can solve the problems of increased pressure during the stroke, increased cost of piston rod manufacture, and increased cost of bores, etc., to achieve less cost, improve guided movement, and the effect of length
- Summary
- Abstract
- Description
- Claims
- Application Information
AI Technical Summary
Benefits of technology
Problems solved by technology
Method used
Examples
Embodiment Construction
[0019]Referring in more detail to the drawings, FIGS. 1 and 2 illustrate one presently preferred embodiment of a gas spring 10, such as those used in mechanical presses (not shown). Generally, a plurality of gas springs 10 may be disposed in the mechanical press such that a piston rod 12 of each gas spring 10 is engaged and driven by a ram of the press as the ram advances to form a sheet metal blank in a die assembly of the press.
[0020]The gas spring has a casing 14 with a generally cylindrical wall 16 terminating at a generally closed end 18, and at another end 20 that is substantially open for receiving the piston rod 12 therein. Generally, the closed end 18 is attached, for example through a weld joint, or formed as one piece with the cylindrical wall 16. The wall 16 of the casing 14 has an inner surface 22 defining at least in part a gas chamber 24, and an outer surface 26. The inner surface 22 of the wall 16 has a circumferential retainer groove 28 constructed for receipt of a ...
PUM
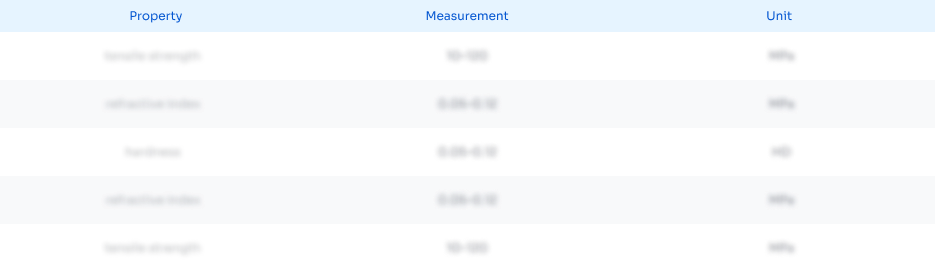
Abstract
Description
Claims
Application Information
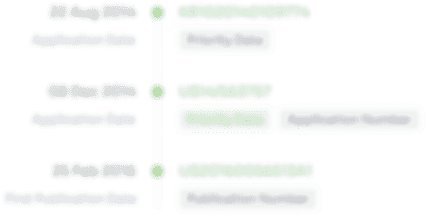
- R&D Engineer
- R&D Manager
- IP Professional
- Industry Leading Data Capabilities
- Powerful AI technology
- Patent DNA Extraction
Browse by: Latest US Patents, China's latest patents, Technical Efficacy Thesaurus, Application Domain, Technology Topic.
© 2024 PatSnap. All rights reserved.Legal|Privacy policy|Modern Slavery Act Transparency Statement|Sitemap