Method for Producing Ceramic Layers
a technology of ceramic layers and layers, applied in the direction of pretreatment surfaces, coatings, pressure inorganic powder coatings, etc., can solve the problem of not reaching the melting temperature of particles, and achieve the effect of reducing internal stresses, reducing or even eliminating the development of manufacturing stresses, and efficient methods
- Summary
- Abstract
- Description
- Claims
- Application Information
AI Technical Summary
Benefits of technology
Problems solved by technology
Method used
Image
Examples
Embodiment Construction
[0021]The apparatus of FIG. 1 features a vacuum container 11 in which are disposed on one side a cold-spray nozzle 12 that can also be designated as a cold gas spray gun and on the other side a substrate 13 (fixings not shown in greater detail). A process gas can be supplied to the cold gas spray gun 12 via a first line 14. As indicated by the contour, said nozzle has a de Laval form through which the process gas is expanded and accelerated toward a surface 16 of the substrate 13 in the form of a gas jet (arrow 15). The process gas can contain oxygen 17 as a reactive gas, for example. Moreover, the process gas can be heated in a manner which is not shown, thereby setting a required process temperature in the vacuum container 11.
[0022]Particles 19, which can be implemented as a matrix of pre-ceramic polymers 19a with filling materials 19b for the polymer ceramic that is to be formed, can be supplied to the cold-spray nozzle 12 via a second line 18. These particles are accelerated in the
PUM
Property | Measurement | Unit |
---|---|---|
Adhesion strength | aaaaa | aaaaa |
Energy | aaaaa | aaaaa |
Electromagnetism | aaaaa | aaaaa |
Abstract
Description
Claims
Application Information
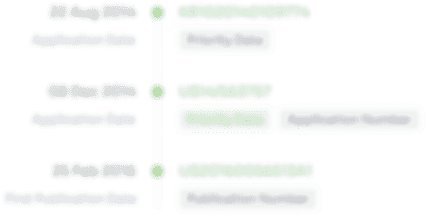
- R&D Engineer
- R&D Manager
- IP Professional
- Industry Leading Data Capabilities
- Powerful AI technology
- Patent DNA Extraction
Browse by: Latest US Patents, China's latest patents, Technical Efficacy Thesaurus, Application Domain, Technology Topic.
© 2024 PatSnap. All rights reserved.Legal|Privacy policy|Modern Slavery Act Transparency Statement|Sitemap