System and method for inspection of parts with complex geometries
a geometrie and complex technology, applied in the field of systems for detecting parts flaws, can solve the problems of early failure of critical areas of engine components, failure of engine components, and poor detectability of eddy current inspection
- Summary
- Abstract
- Description
- Claims
- Application Information
AI Technical Summary
Problems solved by technology
Method used
Examples
Embodiment Construction
[0016]As discussed in detail below, embodiments of the invention are directed to a system and method for inspection of parts with complex geometries. As used herein, the term “inspection” includes inspection for detecting flaws in a complex surface and a sub-surface region of the parts such as, but not limited to, internal cracks, external cracks and pits. A non-limiting example of the part includes an airfoil (turbine blade) in an aircraft engine. It should be appreciated that the methods and apparatus can be applied to a wide variety of components used within an aircraft engine, a steam turbine, a nuclear power plant, an automotive engine, or to inspect any mechanical component.
[0017]FIG. 1 is a schematic illustration of a multi-dimensional array probe system 10 for inspecting a part 11 having a contoured surface 12. The system 10 includes a multi-dimensional array of eddy current sensors 13 disposed on a flexible grid 14. The multi-dimensional array of eddy current sensors 13 are...
PUM
Property | Measurement | Unit |
---|---|---|
coverage | aaaaa | aaaaa |
critical area | aaaaa | aaaaa |
fluorescent penetrant inspection | aaaaa | aaaaa |
Abstract
Description
Claims
Application Information
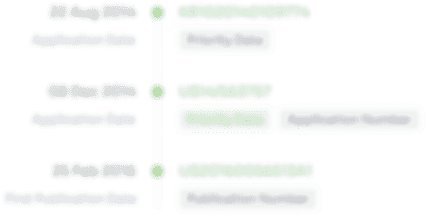
- R&D Engineer
- R&D Manager
- IP Professional
- Industry Leading Data Capabilities
- Powerful AI technology
- Patent DNA Extraction
Browse by: Latest US Patents, China's latest patents, Technical Efficacy Thesaurus, Application Domain, Technology Topic.
© 2024 PatSnap. All rights reserved.Legal|Privacy policy|Modern Slavery Act Transparency Statement|Sitemap