Composite sound-absorbing device with built in resonant cavity
a sound-absorbing device and cavity technology, applied in the field of composite sound-absorbing devices with built-in resonant cavities, can solve the problems of not being wide enough, unable to meet some practical needs of noise control engineering, and being almost impossible to realize in practice, so as to increase the acoustic impedance of the perforated board, and consume enough acoustic energy
- Summary
- Abstract
- Description
- Claims
- Application Information
AI Technical Summary
Benefits of technology
Problems solved by technology
Method used
Image
Examples
embodiment one
[0036]Referring to FIG. 1, the embodiment provides a composite sound-absorbing device with built-in resonant cavity. The device comprises a closed cavity formed by a perforated board 1, a back board 2 and side boards 3 all made up of stainless steel, wherein the depth D of the closed cavity is 40 mm. The perforated board 1 is a square board with the length of the side being 80 mm and the thickness being 5 mm. On the perforated board 1, first pores 6, with a diameter of 3 mm, are formed. The perforation rate σ of the first pores 6 is 28%. The first pores 6 are regularly arranged in the pattern of a square on the perforated board 1. In the closed cavity, four resonant cavities 5 are formed, with each resonant cavity 5 being made of aluminum and having a shape of sphere. The volume of the resonant cavity 5 is 1.4×104 mm3 and the thickness of the wall of the resonant cavity 5 is 5 mm. Moreover, on the wall of the resonant cavity 5, a second pore 6′, with a diameter of 2 mm, is formed. The
embodiment two
[0037]Referring to FIG. 2, the present embodiment provides a composite sound-absorbing device with built-in resonant cavity according to the present invention. The device comprises a closed cavity formed by a perforated board 1, a back board 2 and side boards 3 all made of stainless steel, wherein the depth D of the closed cavity is 50 mm. The perforated board 1 is a round board, with a diameter of 100 mm and a thickness of 0.7 mm. On the perforated board 1, first pores 6, with a diameter of 1.7 mm, are formed. The perforation rate σ of the first pores 6 is 4.6%. The first pores 6 are arranged regularly in the pattern of a square on the perforated board 1. In the closed cavity, four resonant cavities are formed, with each resonant cavity being made of plastic. The volume of the resonant cavity 5 is 3.35×104 mm3 and the thickness of the wall of the resonant cavity 5 is 0.4 mm. Furthermore, there are 26 second pores 6′ on the wall of the resonant cavity 5, evenly distributed on the circu
embodiment three
[0042]Referring to FIG. 2, the embodiment provides a composite sound-absorbing device with built-in resonant cavity. The device comprises a closed cavity formed by a perforated board 1, a back board 2 and side boards 3 all made up of stainless steel, with the depth D of the closed cavity being 100 mm. The perforated board 1 is a round board, with a diameter of 100 mm and thickness of 0.7 mm. On the perforated board 1, first pores 6, with a diameter of 1.7 mm are formed. The perforation rate of the first pores 6 is 4.6%. The first pores 6 are arranged regularly in a pattern of square on the perforated board 1. Separately, nine, seven, four and one resonant cavity 5, made of plastic and having a shape of sphere and a volume V of 3.35×104 mm3 and the thickness of the wall of the resonant cavity 5 being 0.4 mm, is arranged in the closed cavity. Furthermore, there are 26 second pores 6′ on the wall of the resonant cavity 5, evenly distributed on the circumferences of three mutually perpendi
PUM
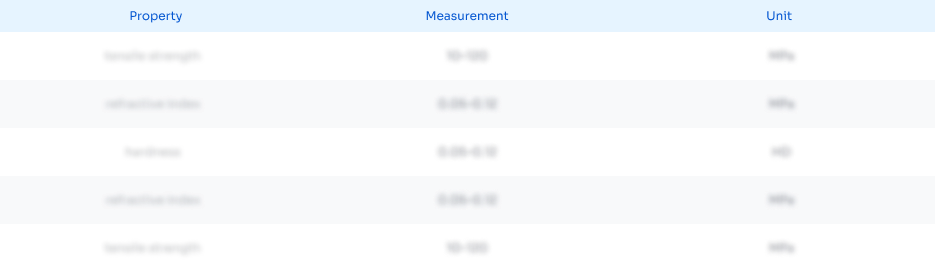
Abstract
Description
Claims
Application Information
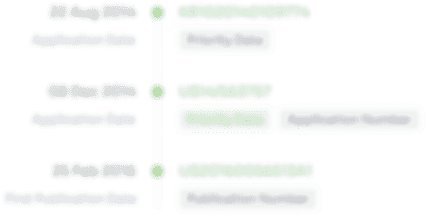
- R&D Engineer
- R&D Manager
- IP Professional
- Industry Leading Data Capabilities
- Powerful AI technology
- Patent DNA Extraction
Browse by: Latest US Patents, China's latest patents, Technical Efficacy Thesaurus, Application Domain, Technology Topic.
© 2024 PatSnap. All rights reserved.Legal|Privacy policy|Modern Slavery Act Transparency Statement|Sitemap