Photosensitive resin composition and applications thereof
a technology of photosensitive resin and composition, applied in the field of photosensitive resin composition, can solve the problems of high linear thermal expansion coefficient, adversely affecting process accuracy, damage to optical devices, etc., and achieve the effect of low linear thermal expansion coefficient and good cross-sectional shap
- Summary
- Abstract
- Description
- Claims
- Application Information
AI Technical Summary
Benefits of technology
Problems solved by technology
Method used
Image
Examples
examples
Preparation of Alkali-Soluble Resin (A)
synthesis example a-1
[0152]A 1000 ml four-necked flask, which is equipped with a nitrogen inlet, a stirrer, a heater, a condenser, and a thermometer, was introduced with nitrogen gas and was added with methacrylic acid (referred as MMA, 10 parts by weight), glycidyl methacrylate (referred as GMA, 65 parts by weight), dicyclopentanyl methacrylate (referred as FA-513M, 15 parts by weight), styrene (referred as SM, 10 parts by weight), and diethylene glycol dimethyl ether as a solvent (referred as Diglyme, 240 parts by weight) to form a mixture.
[0153]When the four-necked flask was filled with nitrogen gas, the mixture was stirred and heated up to 85° C. in an oil bath. A catalyst solution (3.0 parts by weight of 2,2′-azobis(2,4-dimethylvaleronitrile)(referred as ADVN) dissolved in 20 parts by weight of Diglyme) was divided into 5 parts and was added sequentially into the four-necked flask part by part within an hour for inducing a polymerization reaction. The polymerization reaction was then conducted at 70°
synthesis example a-2
[0154]A 1000 ml four-necked flask, which is equipped with a nitrogen inlet, a stirrer, a heater, a condenser, and a thermometer, was introduced with nitrogen gas and was added with 2-methacryloyloxyethyl succinate monoester (referred as HOMS, 40 parts by weight), 3,4-epoxycyclohexylmethyl methacrylate (referred as EC-MAA, 25 parts by weight), 2-hydroxyethyl methacrylate (referred as HEMA, 5 parts by weight), FA-513M (10 parts by weight), SM (20 parts by weight), and propylene glycol monomethyl ether acetate as a solvent (referred as PGMEA, 240 parts by weight) to form a mixture.
[0155]When the four-necked flask was filled with nitrogen gas, the mixture was stirred and heated up to 85° C. in an oil bath. A catalyst solution (2.4 parts by weight of ADVN dissolved in 20 parts by weight of PGMEA) was divided into 5 parts and was added sequentially into the four-necked flask part by part within one hour for inducing a polymerization reaction. The polymerization reaction was then conducted at
PUM
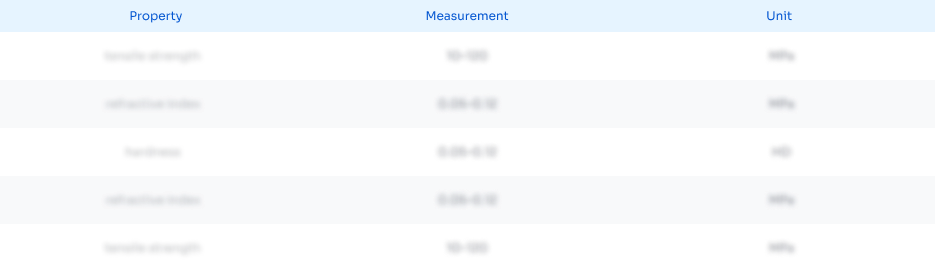
Abstract
Description
Claims
Application Information
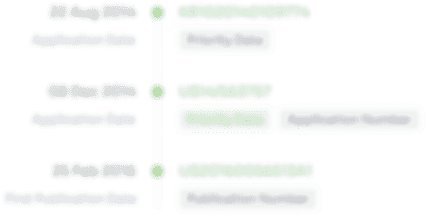
- R&D Engineer
- R&D Manager
- IP Professional
- Industry Leading Data Capabilities
- Powerful AI technology
- Patent DNA Extraction
Browse by: Latest US Patents, China's latest patents, Technical Efficacy Thesaurus, Application Domain, Technology Topic.
© 2024 PatSnap. All rights reserved.Legal|Privacy policy|Modern Slavery Act Transparency Statement|Sitemap