A process for reacting oxygen carrying regenerated catalyst prior to use in a fluidized bed reactor
a technology of regenerated catalyst and reaction process, which is applied in the direction of catalyst regeneration/reactivation, physical/chemical process catalyst, metal/metal-oxide/metal-hydroxide catalyst, etc., can solve the problems of oxygen being transferred to the dehydrogenation reactor, increasing the operating cost due to nitrogen consumption, and degrading valuable feedstock to less valuable products
- Summary
- Abstract
- Description
- Claims
- Application Information
AI Technical Summary
Benefits of technology
Problems solved by technology
Method used
Image
Examples
##ventive example 1
Inventive Example 1
Methane as a Fuel Source
[0026]The data in Table 1 was collected on a vertical 36-inch quartz glass reactor with an internal diameter of 1.5 inches. The reactor was loaded with 50 grams of dehydrogenation catalyst, having the following composition: In preferred embodiments, the catalyst comprises from 0.1 to 34 wt %, preferably 0.2 to 3.8 wt %, gallium oxide (Ga2O3); from 1 to 300 parts per million (ppm), preferably 50 to 300 ppm, by weight platinum; from 0 to 5 wt %, preferably 0.01 to 1 wt %, of an alkaline and / or earth-alkaline such as potassium; from 0.08 to 3 wt % silica; and the balance to 100 wt % being alumina, which resulted on a catalyst bed height of 2.2 inches. The inlet gas was introduced at the bottom of the reactor and a quartz frit was used to distribute the gas flow across the reactor diameter. The volumetric flow of the inlet gas was 1100 standard cubic centimeters per minute. The inlet gas flow caused the catalyst to fluidize. The inlet gas compos
##ventive example 2
Inventive Example 2
Catalyst Coke Residue as a Fuel
[0027]Tests were carried out in a thermogravimetric analyzer to determine the combustion rate of coke on the catalyst, as described above. A catalyst with coke was heated up in argon to the target temperature. When the target temperature was achieved, air was fed to the unit and the mass rate of change was measured. The resulting data are shown in Table 3. The catalyst with coke was prepared under the following conditions: in the reactor as described above, 1 g of catalyst with no diluent was loaded in the reactor and topped off reactor with 2 mm×2 mm quartz stock and the reactor run for 1 hour at 700° C.; Propane flow of 46.24 sccm; Nitrogen flow of 5.14 sccm; and WHSV of 5 1 / hr.
TABLE 3Temperature, ° C.Coke Combustion Rate, lb O2 / sec / lb catalyst5000.00016000.00177000.0020
[0028]In order to calculate the required time to burn the oxygen out of the regenerated catalyst stream, the following example is presented. If 100 lb / hr of ox
PUM
Property | Measurement | Unit |
---|---|---|
Temperature | aaaaa | aaaaa |
Temperature | aaaaa | aaaaa |
Temperature | aaaaa | aaaaa |
Abstract
Description
Claims
Application Information
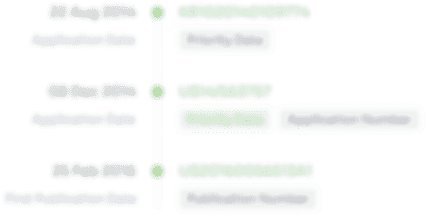
- R&D Engineer
- R&D Manager
- IP Professional
- Industry Leading Data Capabilities
- Powerful AI technology
- Patent DNA Extraction
Browse by: Latest US Patents, China's latest patents, Technical Efficacy Thesaurus, Application Domain, Technology Topic.
© 2024 PatSnap. All rights reserved.Legal|Privacy policy|Modern Slavery Act Transparency Statement|Sitemap