Multi-piece fastener with self-indexing nut
a multi-piece, self-indexing technology, applied in the direction of screw, load-modified fastener, coupling, etc., can solve the problems of difficult installation, difficult positioning of traditional attachment methods and fasteners in such regions, and poor ergonomics
- Summary
- Abstract
- Description
- Claims
- Application Information
AI Technical Summary
Problems solved by technology
Method used
Examples
Embodiment Construction
[0024]Referring now to FIG. 1, which is an illustration of an aircraft 10 in accordance with the present invention. The aircraft 10 is comprised of a plurality of joint assemblies wherein traditional fastening and assembly techniques may unfeasible or cost prohibitive. One such joint assembly is referred to as the wing side-of-body joint assembly 12, see FIG. 2. The wing side-of-body joint assembly 12 is located where the wing 14 joints the aircraft body side 16. This joint assembly 12 is very important as it is used to join a variety of structures together to form a reliable joint that is preferably highly resistant to joint fatigue.
[0025]As illustrated in FIG. 2, the joint assembly 12 is used to join a variety of different structures. Aluminum or titanium chords 18, also referred to as a first joint element, are utilized to join primary structures such as aluminum or carbon fiber-reinforced composite skin elements 20, also referred to as a second joint element, stringers 22, strin...
PUM
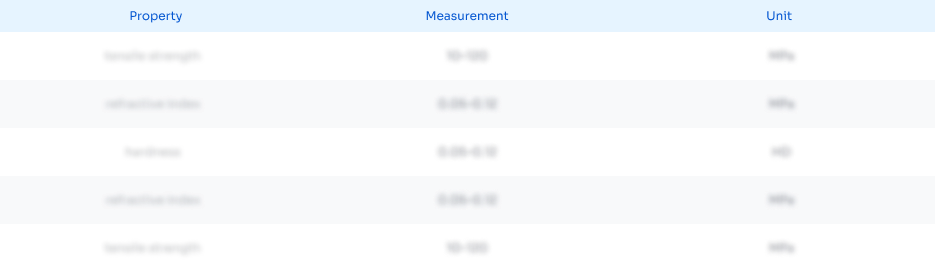
Abstract
Description
Claims
Application Information
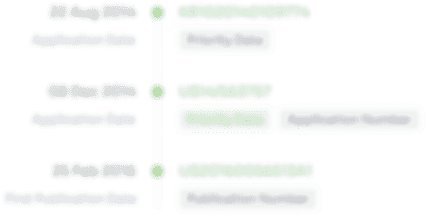
- R&D Engineer
- R&D Manager
- IP Professional
- Industry Leading Data Capabilities
- Powerful AI technology
- Patent DNA Extraction
Browse by: Latest US Patents, China's latest patents, Technical Efficacy Thesaurus, Application Domain, Technology Topic.
© 2024 PatSnap. All rights reserved.Legal|Privacy policy|Modern Slavery Act Transparency Statement|Sitemap