Process for pressing galvanized PCB boards and multi-layer PCB board
A PCB board and process technology, which is applied in the lamination process and multi-layer PCB board field, can solve the problems of PCB board short circuit, waste of processing resources, easy copper penetration, etc., and achieve the effect of preventing glue shortage and avoiding waste of processing resources
- Summary
- Abstract
- Description
- Claims
- Application Information
AI Technical Summary
Benefits of technology
Problems solved by technology
Method used
Image
Examples
Embodiment Construction
[0020] Refer below Figure 3-Figure 6 An embodiment of the lamination process after electroplating of the PCB provided by the present invention is described in detail.
[0021] In this embodiment, the sequential pressing process mainly includes the following steps:
[0022] refer to image 3 , in the first pressing step, after the lower core board assembly 101 to be pressed is sequentially covered with a layer of insulating leakage trap 201, a layer of spacer 301, and a layer of heat-resistant and pressure-resistant elastic gasket 501, the Under the condition of high temperature and high pressure, the lower core board assembly 101 and the upper layer core board assembly 102 are pressed together, and the adhesive sheet 301 is pressed into the groove 14 between the copper foil lines on the surface of the lower core board assembly 101. The deformation of the pressure-resistant elastic gasket 501 can press the insulating leak trap 201 into the groove between the copper foil lines 1
PUM
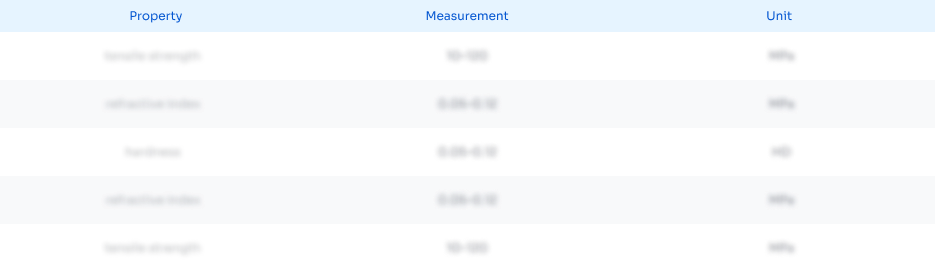
Abstract
Description
Claims
Application Information
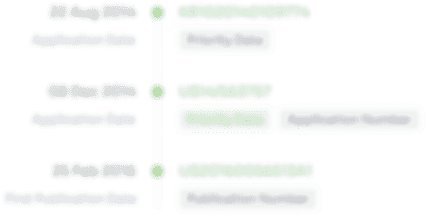
- R&D Engineer
- R&D Manager
- IP Professional
- Industry Leading Data Capabilities
- Powerful AI technology
- Patent DNA Extraction
Browse by: Latest US Patents, China's latest patents, Technical Efficacy Thesaurus, Application Domain, Technology Topic.
© 2024 PatSnap. All rights reserved.Legal|Privacy policy|Modern Slavery Act Transparency Statement|Sitemap