Preparation method of nano epoxy resin composite material
A nano-composite material and epoxy resin technology, applied in the direction of epoxy resin coating, epoxy resin glue, adhesive type, etc., can solve the problems of high cost, high density, and difficult degradation of composite materials, and achieve less pollution, Improve the effect of bending strength and fracture bending deformation, excellent mechanical properties and dimensional stability
- Summary
- Abstract
- Description
- Claims
- Application Information
AI Technical Summary
Problems solved by technology
Method used
Examples
Example Embodiment
[0028] Example 1:
[0029] A preparation method of epoxy resin nanocomposite material, which comprises the following steps:
[0030] 1) Pretreatment of raw materials: Liquid epoxy resin E51 (epoxy value between 0.48~0.52mol / 100g) is vacuum dried at 50℃ to remove water (vacuum degree is -0.1MPa), vacuum drying time for water removal 120min, until the liquid epoxy resin becomes clear and no bubbles emerge;
[0031] Diethylenetriamine (curing agent) is purified by vacuum distillation before use (collecting the fraction at 85-90°C under a vacuum of -0.098MPa) to make the curing agent purity ≥95wt%;
[0032] 2) Extraction of starch nanocrystals by the action of sulfuric acid solution: press H 2 SO 4 The ratio of solution, pea starch, and deionized water is 250mL: 36.00g: 100mL, and 3.16mol / L H is selected 2 SO 4 Solution, pea starch and deionized water, spare;
[0033] Add pea starch to 3.16mol / L H 2 SO 4 The solution container; place the container in an oil bath at 40°C and mechanically
Example Embodiment
[0040] Example 2:
[0041] A preparation method of epoxy resin nanocomposite material, which comprises the following steps:
[0042] 1) Pretreatment of raw materials: Bisphenol A epoxy resin E51 is vacuum dried at 100°C to remove water (vacuum degree is -0.1MPa), and the vacuum drying time is 180min until the liquid epoxy resin becomes clear And no bubbles come out;
[0043] Diethylenetriamine (curing agent) is purified by vacuum distillation before use (collecting the fractions around 85-90°C under a vacuum of -0.098MPa) to make the curing agent purity ≥95wt%; the curing agent can be diethylenetriamine Any of aliphatic polyamines such as amine, triethylenetetramine, tetraethylenepentamine, or diethylaminopropylamine.
[0044] 2) First prepare 250mL 3.16mol / L H 2 SO 4 The solution, when the temperature of the sulfuric acid solution drops to room temperature, transfer it to a 500 mL round bottom flask. Weigh 36.00g of dry pea starch raw material, add it to the above mentioned 3.16mol
Example Embodiment
[0048] Example 3:
[0049] As in Example 1, the mass ratio of epoxy resin E51:starch nanocrystals in the third step {ie step 3)} was changed to 100:1.5, and the oil bath temperature, stirring rate, stirring time and ultrasonic time were changed to 60°C. , 800rpm, 50min and 30min; the stirring time and vacuum degassing time of the fourth step were changed to 10min and 10min respectively; the degassing time of the fifth step was changed to 10min, curing at room temperature for 3d, and curing at 90℃ for 8h.
PUM
Property | Measurement | Unit |
---|---|---|
Epoxy value | aaaaa | aaaaa |
Abstract
Description
Claims
Application Information
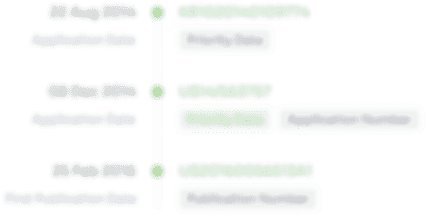
- R&D Engineer
- R&D Manager
- IP Professional
- Industry Leading Data Capabilities
- Powerful AI technology
- Patent DNA Extraction
Browse by: Latest US Patents, China's latest patents, Technical Efficacy Thesaurus, Application Domain, Technology Topic.
© 2024 PatSnap. All rights reserved.Legal|Privacy policy|Modern Slavery Act Transparency Statement|Sitemap