Impermeable concrete and preparation method thereof
A technology of anti-seepage concrete and cement, which is applied in the field of building anti-seepage, can solve the problems of building materials usage, difficulty in decomposition, and small size, and achieve the effects of reducing project cost, improving mechanical properties, and reducing the degree of damage
- Summary
- Abstract
- Description
- Claims
- Application Information
AI Technical Summary
Problems solved by technology
Method used
Examples
Example Embodiment
[0033]Example 1
[0034]Preparation method of anti-seepage concrete, including the steps of:
[0035]1. Cut the waste tire and milled into the rubber particles of 60 mesh, granite wasteland powder, manufactured by the Shandong Stone Factory, cement adopts the P · O42.5 cement, and the grain size is 6mm ~ 10mm gravel, minus The aquifer is used in a polycarboxylic acid-based water reduction (industrial stage), and the water reduction rate is 20%.
[0036]2. Concrete composition and match ratios: Cement: Water: Sand: Gravel: water reduction = 1: 0.3: 1.2: 2.8: 0.01, with meter according to the above proportion of 20 kg, water 6 kg, sand 24 kg, 56 kg of gravel, 0.2 kg of water reduction agent.
[0037]3. Put 11 kilograms of rubber particles in an alkaline solution (a KOH solution concentration of 15%) for 30 minutes, and remove the water to wash and dry dry.
[0038]4. Pour 20 kg of cement into a water of 6 kg, stir well using a cement mixer.
[0039]5. A 1 kg of nano silica, 10 kg of granite powder is mixe
Example Embodiment
[0041]Example 2
[0042]Preparation method of anti-seepage concrete, including the steps of:
[0043]1. Cut the waste tire and crushed into the rubber particles of the particle size of 70. The granite waste stone powder is manufactured by Shandong Stone Plant. The cement uses P · O42.5 cement, and the grain size is 6mm ~ 10mm gravel, minus The aquifer is used in a polycarboxylic acid-based water reduction (industrial stage), and the water reduction rate is 20%. .
[0044]2. Concrete composition and match ratios: Cement: Water: Sand: Gravel: water reduction = 1: 0.3: 1.2: 2.8: 0.01, with meter according to the above proportion of 20 kg, water 6 kg, sand 24 kg, 56 kg of gravel, 0.2 kg of water reduction agent.
[0045]3. A 14 kg of rubber particles were placed in an alkaline solution (a KOH solution of 15%) for 30 minutes and removed with water to wash and dry drying.
[0046]4. Pour 20 kg of cement into a water of 6 kg, stir well using a cement mixer.
[0047]5. After mixing 1.2 kg of nano silica, 10 kg
Example Embodiment
[0049]Example 3
[0050]Preparation method of anti-seepage concrete, including the steps of:
[0051]1. Cut the waste tire and crush into the rubber particles of the particle size of 80. The granite waste stone powder is manufactured in Shandong Stone Plant. The cement uses P · O42.5 cement, and the grain is 6mm ~ 10mm gravel, minus The aquifer is used in a polycarboxylic acid-based water reduction (industrial stage), and the water reduction rate is 20%. .
[0052]2. Concrete composition and match ratios: Cement: Water: Sand: Gravel: water reduction = 1: 0.3: 1.2: 2.8: 0.01, with meter according to the above proportion of 20 kg, water 6 kg, sand 24 kg, 56 kg of gravel, 0.2 kg of water reduction agent.
[0053]3. Put 13 kilograms of rubber particles into an alkaline solution (15% KOH solution) soaked for 30 minutes, and take it out, rinse with water, and dry.
[0054]4. Pour 20 kg of cement into 6 kg of water and use a cement mixer to fully mix.
[0055]5. Mix 1 kg of nano-silica, 11 kg of granite powder
PUM
Property | Measurement | Unit |
---|---|---|
Particle size | aaaaa | aaaaa |
Particle size | aaaaa | aaaaa |
Particle size | aaaaa | aaaaa |
Abstract
Description
Claims
Application Information
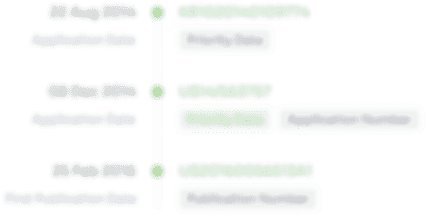
- R&D Engineer
- R&D Manager
- IP Professional
- Industry Leading Data Capabilities
- Powerful AI technology
- Patent DNA Extraction
Browse by: Latest US Patents, China's latest patents, Technical Efficacy Thesaurus, Application Domain, Technology Topic.
© 2024 PatSnap. All rights reserved.Legal|Privacy policy|Modern Slavery Act Transparency Statement|Sitemap