Method for producing polyvinyl alcohol resin
The technology of a polyvinyl alcohol resin and a manufacturing method, which is applied to the manufacturing field of polyvinyl alcohol resin, can solve problems such as content, and achieve the effects of improving washing efficiency, reducing dosage, and efficiently removing
- Summary
- Abstract
- Description
- Claims
- Application Information
AI Technical Summary
Benefits of technology
Problems solved by technology
Method used
Image
Examples
no. 1 Embodiment approach )
[0024] First, the manufacturing method of the PVA resin which concerns on 1st Embodiment of this invention is demonstrated. figure 1 It is a flowchart which shows the manufacturing method of the PVA resin of this embodiment. Such as figure 1 As shown, in the manufacturing method of the PVA resin of this embodiment, each process of a polymerization process (step S1), a saponification process (step S2), a washing process (step S3), and a drying process (step S4) is implemented sequentially.
[0025] [polymerization process]
[0026] In the polymerization process of step S1, one or more than two kinds of vinyl esters are polymerized, or vinyl esters and other monomers that can be copolymerized with them are copolymerized to obtain polyvinyl esters. Examples of the vinyl ester used here include vinyl formate, vinyl acetate, vinyl propionate, vinyl valerate, vinyl caprate, vinyl laurate, vinyl stearate, and vinyl benzoate. , trimethylvinyl acetate, vinyl tert-carbonate, etc., vin
no. 2 Embodiment approach )
[0048] Next, the manufacturing method of the PVA resin which concerns on the 2nd Embodiment of this invention is demonstrated. In this embodiment, the PVA obtained through the saponification process is prepared into a slurry for periodic washing, and the slurry contains methyl acetate: 1-40 parts by mass, methanol: 50-98.9 parts by mass and water: 0.1 ~10 parts by mass of the washing liquid, and the solid content concentration is 1~30% by mass. In addition, the "polymerization process", "saponification process", and "drying process" in the manufacturing method of the PVA resin of this embodiment are the same as that of the said 1st embodiment.
[0049] figure 2 It is a block schematic diagram which shows the washing process in the manufacturing method of the PVA resin of this embodiment. In the method for producing a PVA resin according to the present embodiment, the number of washings is not particularly limited, but it is desirable to perform washing three or more times in o
Embodiment
[0058] Next, the effects of the present invention will be specifically described with reference to Examples and Comparative Examples of the present invention. In this example, polyvinyl alcohol resin was produced by changing washing conditions, and the volatile components contained therein and the amount of residual sodium acetate were measured. Specifically, first, a methanol solution (concentration: 3% by mass) of sodium hydroxide was added to polyvinyl acetate: 37.5 parts by mass, methanol: 62.2 parts by mass, and water: 0.2 parts by mass, and saponified at 50° C., A PVA with an average degree of polymerization of 1700 and a degree of saponification of 99 mol% was obtained.
[0059] Then, the PVA obtained by saponification and the washing solution formed by methyl acetate, methanol and water are put into a washing tank with a capacity of 100L, and the slurry of the composition shown in the following Tables 1 and 2 is prepared, according to the following The number of washing
PUM
Property | Measurement | Unit |
---|---|---|
Saponification degree | aaaaa | aaaaa |
Abstract
Description
Claims
Application Information
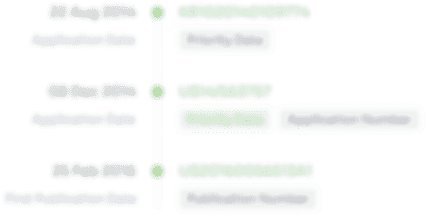
- R&D Engineer
- R&D Manager
- IP Professional
- Industry Leading Data Capabilities
- Powerful AI technology
- Patent DNA Extraction
Browse by: Latest US Patents, China's latest patents, Technical Efficacy Thesaurus, Application Domain, Technology Topic.
© 2024 PatSnap. All rights reserved.Legal|Privacy policy|Modern Slavery Act Transparency Statement|Sitemap