Preparation method of anode material LiMxNiyMn2-x-yO4
A positive electrode material and slurry technology, which is applied in the field of high-voltage positive electrode materials for lithium-ion batteries, can solve problems such as difficult process control, poor electrochemical performance, and inconsistent crystallinity, and the time to achieve high-temperature tempering treatment is short, which is conducive to industrialization The effect of high production and product consistency
- Summary
- Abstract
- Description
- Claims
- Application Information
AI Technical Summary
Benefits of technology
Problems solved by technology
Method used
Image
Examples
Embodiment 1
[0043] In this example, LiNi 0.4 mn 1.6 o 4 The processing steps of the preparation method are as follows:
[0044] (1) Preparation of precursor slurry
[0045] According to the chemical formula LiNi 0.4 mn 1.6 o 4 The ratio of LiNO 3 3.4475g (the molar weight of Li is 0.05mol), Mn(NO 3 ) 2 4H 2 O 20.0008g (the molar weight of Mn is 0.08mol), Ni(NO 3 ) 2 ·6H 2 O 5.8162g (the molar weight of Ni is 0.02mol) is added in the reactor, then distilled water is added to form a mixed solution, and the amount of distilled water added is limited to the complete dissolution of each component; glucose 4.5g (0.025mol) is weighed and Put it into a container, add distilled water to form a glucose solution, the amount of distilled water added is limited to the complete dissolution of glucose; pour the glucose solution into the mixed solution, first stir at normal pressure and 50°C for 10h, and then heat up to 90°C ℃ and stirred until foaming (about 2 hours), to obtain the precursor
Embodiment 2
[0054] In this example, LiCr 0.2 Ni 0.4 mn 1.4 o 4 The processing steps of the preparation method are as follows:
[0055] (1) Preparation of precursor slurry
[0056] According to the chemical formula LiCr 0.2 Ni 0.4 mn 1.4 o 4 The ratio of LiNO 3 3.4475g (the molar weight of Li is 0.05mol), Mn(CH 3 COO) 2 4H 2 O 17.1563g (the molar amount of Mn is 0.07mol), Ni(NO 3 ) 2 ·6H 2 O 5.8162g (the molar weight of Ni is 0.02mol), Cr(CH 3 COO) 3 2.2913g (the molar weight of Cr is 0.01mol) is added in the reactor, and then deionized water is added to form a mixed solution. The amount of deionized water added is limited to the complete dissolution of each component; weigh 26.2675g of citric acid ( 0.125mol) and put it into a container, add deionized water to form a citric acid solution, the amount of deionized water added is limited to the complete dissolution of citric acid; pour the citric acid solution into the mixed solution, , Stir at 95°C until foaming (about 1.5 h
Embodiment 3
[0064] In this example, LiCo 0.2 Ni 0.4 mn 1.4 o 4 The processing steps of the preparation method are as follows:
[0065] (1) Preparation of precursor slurry
[0066] According to the chemical formula LiCo 0.2 Ni 0.4 mn 1.4 o 4 The matching ratio, the CH 3 COOLi 6.5990g (the molar weight of Li is 0.1mol), Mn(NO 3 ) 2 4H 2 O 35.0014g (the molar weight of Mn is 0.14mol), Ni(CH 3 COO) 2 4H 2 O 9.9544g (the molar weight of Ni is 0.04mol), Co(NO 3 ) 2 ·6H 2 O 5.821g (the molar weight of Co is 0.02mol) was added in the reactor, and then deionized water was added to form a mixed solution. The amount of deionized water added was limited to the complete dissolution of each component; 12.012g of urea was weighed ( 0.2mol) and put it into a container, add deionized water to form a urea solution, the amount of deionized water added is limited to the complete dissolution of urea; pour the urea solution into the mixed solution, Stir until foaming (about 4 hours) to obtain pr
PUM
Property | Measurement | Unit |
---|---|---|
The average particle size | aaaaa | aaaaa |
Abstract
Description
Claims
Application Information
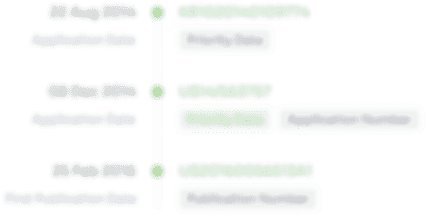
- R&D Engineer
- R&D Manager
- IP Professional
- Industry Leading Data Capabilities
- Powerful AI technology
- Patent DNA Extraction
Browse by: Latest US Patents, China's latest patents, Technical Efficacy Thesaurus, Application Domain, Technology Topic.
© 2024 PatSnap. All rights reserved.Legal|Privacy policy|Modern Slavery Act Transparency Statement|Sitemap