Production technology for casting thin-wall cookware through using precoated sand hot box method
A production process and hot core box technology, which is applied in the direction of manufacturing tools, casting molding equipment, molding machines, etc., can solve the problem of the shape, size and quality of cast iron cookware, the serious dust in the manual clay sand production process, and the difficulty in forming thin-walled castings, etc. problems, to achieve the effects of small casting deformation, high yield and low casting cost
- Summary
- Abstract
- Description
- Claims
- Application Information
AI Technical Summary
Problems solved by technology
Method used
Image
Examples
Embodiment Construction
[0019] Such as Figure 1-3 Shown, a kind of production technology of coated sand hot core box method casting thin-walled cooker, comprises the following steps:
[0020] Step 1. Make a hot core box mold according to the shape of the cooker. There is a negative pressure structure on the mold, and install the hot core box mold on the core shooter;
[0021] Step 2: Inject the coated sand into the hot core box mold, and make the coated sand solidify and form in the hot core box mold through electric heating;
[0022] Step 3: After the core shooter splits the mold, remove the middle template, and then close the mold;
[0023] Step 4: Start the vacuum source first after closing the mold, and pour the molten iron while the vacuum source draws negative pressure on the core shooter. The gas generated during the pouring process is sucked away by the vacuum source. The vacuum source is preferably a vacuum pump;
[0024] In step five, after the casting is cooled, the mold is divided to obta
PUM
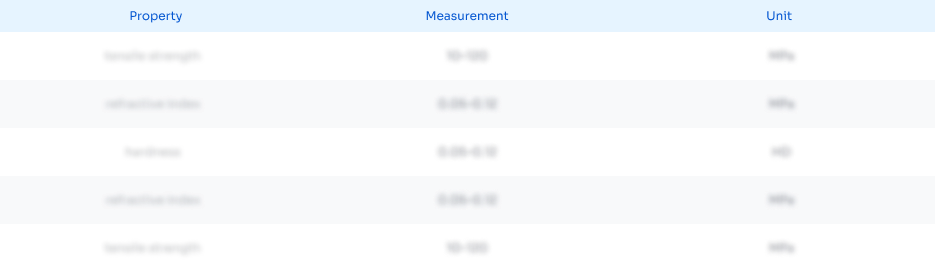
Abstract
Description
Claims
Application Information
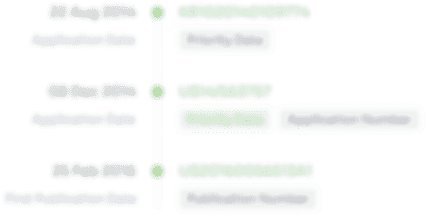
- R&D Engineer
- R&D Manager
- IP Professional
- Industry Leading Data Capabilities
- Powerful AI technology
- Patent DNA Extraction
Browse by: Latest US Patents, China's latest patents, Technical Efficacy Thesaurus, Application Domain, Technology Topic.
© 2024 PatSnap. All rights reserved.Legal|Privacy policy|Modern Slavery Act Transparency Statement|Sitemap