Production method of vanadium nitrogen alloy
A technology of vanadium nitrogen alloy and production method, applied in the field of metal additives, can solve the problems of unstable product quality, large fluctuation of product quality, difficult control of high temperature, etc., and achieve the effects of avoiding product failure, stable product quality and cost saving.
- Summary
- Abstract
- Description
- Claims
- Application Information
AI Technical Summary
Benefits of technology
Problems solved by technology
Method used
Image
Examples
Embodiment 1
[0019] A production method of vanadium nitrogen alloy, the steps of the method are as follows:
[0020] a) Stir and mix the powdered vanadium-containing compound, carbonaceous reducing agent, binder and fluoride mineralizer evenly, and press to form a regular mixed billet, wherein the weight ratio of each component is:
[0021] The vanadium-containing compound uses 139 parts of vanadium pentoxide; the carbonaceous reducing agent uses 44 parts of graphite powder; the binder uses 14 parts of dextrin aqueous solution; the fluoride mineralizer uses 5 parts of sodium fluoride;
[0022] b) Put the obtained mixed blank into a heat-resistant stainless steel container under the protection of nitrogen atmosphere for carbonization reaction pretreatment to obtain a pretreated product, wherein the temperature of the carbonization reaction in the heat-resistant stainless steel container is kept at 590 ° C, and the carbonization reaction time is 3 hours;
[0023] c) Put the pretreated product
Embodiment 2
[0029] A production method of vanadium nitrogen alloy, the steps of the method are as follows:
[0030] a) Stir and mix the powdered vanadium-containing compound, carbonaceous reducing agent, binder and fluoride mineralizer evenly, and press to form a regular mixed billet, wherein the weight ratio of each component is:
[0031] The vanadium-containing compound uses 145 parts of ammonium metavanadate; the carbonaceous reducing agent uses 49 parts of carbon black powder; the binder uses 19 parts of starch aqueous solution; the fluoride mineralizer uses 1 part of potassium fluoride;
[0032] b) Put the obtained mixed blank into a heat-resistant stainless steel container under the protection of nitrogen atmosphere for carbonization reaction pretreatment to obtain a pretreated product, wherein the temperature of the carbonization reaction in the heat-resistant stainless steel container is kept at 775°C, and the carbonization reaction time is 9 hours;
[0033] c) Put the pretreated pr
Embodiment 3
[0039] A production method of vanadium nitrogen alloy, the steps of the method are as follows:
[0040] a) Stir and mix the powdered vanadium-containing compound, carbonaceous reducing agent, binder and fluoride mineralizer evenly, and press to form a regular mixed billet, wherein the weight ratio of each component is:
[0041] The vanadium-containing compound adopts 142 parts of vanadium pentoxide; the carbonaceous reducing agent adopts 47 parts of a mixture of graphite powder and carbon black powder; the binder adopts 16 parts of dextrin aqueous solution; the fluoride mineralizer adopts 4 parts of sodium fluoride;
[0042] b) Put the obtained mixed blank into a heat-resistant stainless steel container protected by a nitrogen atmosphere for carbonization reaction pretreatment to obtain a pretreated product, wherein the temperature of the carbonization reaction in the heat-resistant stainless steel container is kept at 650°C, and the carbonization reaction time is 5 hours;
[00
PUM
Property | Measurement | Unit |
---|---|---|
Apparent density | aaaaa | aaaaa |
Apparent density | aaaaa | aaaaa |
Apparent density | aaaaa | aaaaa |
Abstract
Description
Claims
Application Information
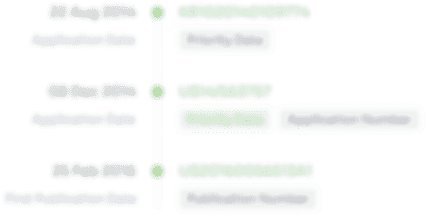
- R&D Engineer
- R&D Manager
- IP Professional
- Industry Leading Data Capabilities
- Powerful AI technology
- Patent DNA Extraction
Browse by: Latest US Patents, China's latest patents, Technical Efficacy Thesaurus, Application Domain, Technology Topic.
© 2024 PatSnap. All rights reserved.Legal|Privacy policy|Modern Slavery Act Transparency Statement|Sitemap