Manufacturing method of high-performance marine concrete
A technology of marine concrete and its production method, which is applied in the field of building materials, can solve the problems of cracking, damage, and falling off of the concrete protective layer, and achieve the effects of reduced apparent density, strong corrosion resistance, and low apparent density
- Summary
- Abstract
- Description
- Claims
- Application Information
AI Technical Summary
Benefits of technology
Problems solved by technology
Method used
Examples
Embodiment 1
[0023] Step 1: Take raw materials according to the following parts by mass:
[0024] Cement: 35,
[0025] Medium coarse sand: 9,
[0026] Gravel: 10,
[0027] Blast Furnace Slag: 20,
[0028] Soot: 13,
[0029] Silica fume: 2,
[0030] Steel bar rust inhibitor: 1.5,
[0031] Water reducer: 0.5;
[0032] Step 2: Take out the medium-coarse sand and put it in water to wash away the dirt on the surface, take out the cleaned medium-coarse sand, put it in a cool place for 20 minutes, and dry the water;
[0033] Step 3: Take out all the cement, put it into a mixer for stirring, put in the washed medium-coarse sand and stir for 3 minutes, so that the cement and medium-coarse sand are fully mixed;
[0034] Step 4: Continue to add gravel, blast furnace slag, coal ash and silica fume to the mixer, and stir the mixture evenly;
[0035] Step 5: Continue to add steel rust inhibitor to the mixer, and add a small amount of water to make the concrete mix evenly, and stir until it becomes
Embodiment 2
[0039] Step 1: Take raw materials according to the following parts by mass:
[0040] Cement: 50,
[0041] Medium coarse sand: 15,
[0042] Gravel: 11,
[0043] Blast Furnace Slag: 26,
[0044] Soot: 19,
[0045] Silica fume: 5,
[0046] Steel bar rust inhibitor: 3,
[0047] Water reducer: 2;
[0048] Step 2: Take out the medium-coarse sand and put it in water to wash away the dirt on the surface, take out the cleaned medium-coarse sand, put it in a cool place for 20 minutes, and dry the water;
[0049] Step 3: Take out all the cement, put it into a mixer for stirring, put in the washed medium-coarse sand and stir for 3 minutes, so that the cement and medium-coarse sand are fully mixed;
[0050] Step 4: Continue to add gravel, blast furnace slag, coal ash and silica fume to the mixer, and stir the mixture evenly;
[0051] Step 5: Continue to add steel rust inhibitor to the mixer, and add a small amount of water to make the concrete mix evenly, and stir until it becomes gel
Embodiment 3
[0055] Step 1: Take raw materials according to the following parts by mass:
[0056] Cement: 40,
[0057] Medium coarse sand: 13,
[0058] Gravel: 10,
[0059] Blast Furnace Slag: 23,
[0060] Soot: 16,
[0061] Silica fume: 3,
[0062] Steel bar rust inhibitor: 2,
[0063] Water reducer: 1.5;
[0064] Step 2: Take out the medium-coarse sand and put it in water to wash away the dirt on the surface, take out the cleaned medium-coarse sand, put it in a cool place for 20 minutes, and dry the water;
[0065] Step 3: Take out all the cement, put it into a mixer for stirring, put in the washed medium-coarse sand and stir for 3 minutes, so that the cement and medium-coarse sand are fully mixed;
[0066] Step 4: Continue to add gravel, blast furnace slag, coal ash and silica fume to the mixer, and stir the mixture evenly;
[0067] Step 5: Continue to add steel rust inhibitor to the mixer, and add a small amount of water to make the concrete mix evenly, and stir until it becomes g
PUM
Property | Measurement | Unit |
---|---|---|
Particle size | aaaaa | aaaaa |
Abstract
Description
Claims
Application Information
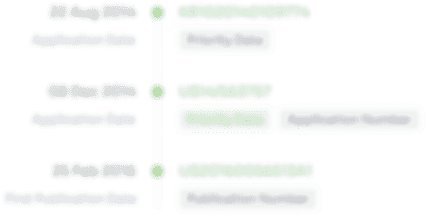
- R&D Engineer
- R&D Manager
- IP Professional
- Industry Leading Data Capabilities
- Powerful AI technology
- Patent DNA Extraction
Browse by: Latest US Patents, China's latest patents, Technical Efficacy Thesaurus, Application Domain, Technology Topic.
© 2024 PatSnap. All rights reserved.Legal|Privacy policy|Modern Slavery Act Transparency Statement|Sitemap